Among machined parts, the machining deformation of CNC-machined aluminum alloy enclosures, especially thin-walled enclosures, is a common technical problem. Let us analyze the causes of deformation, and then take corresponding countermeasures to prevent them.
For aluminum enclosures CNC machining deformation, we summarize the following four points for your reference:
1. The material grade and structural complexity of aluminum will affect the deformation of the enclosures
The deformation of CNC machined aluminum enclosures is related to the complexity of shape, aspect ratio and wall thickness, and is related to the rigidity and stability of aluminum alloy grades.
Therefore, when designing the aluminum enclosures, the influence of these factors on the deformation of the aluminum alloy workpiece should be reduced as much as possible. Especially when the aluminum alloy enclosure with larger size is processed and customized, the structure should be reasonable.
The hardness and looseness of aluminum alloy material blanks should be strictly inspected before machining to ensure the quality of the blanks and reduce the possibility of deformation of aluminum custom parts.
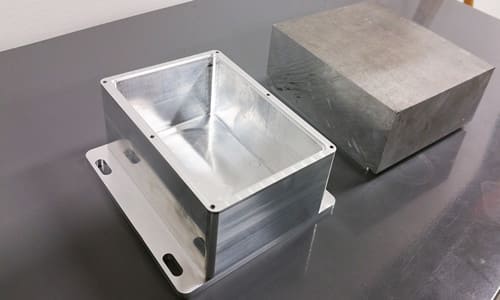
2. The deformation of the aluminum enclosures caused by the machining and clamping of the CNC machining center
When clamping the material blank during the machining of the aluminum enclosure, first select the correct clamping surface, and then give the appropriate clamping force according to the position of the clamping surface.
Therefore, the clamping surface and the force-bearing surface should be made equal as much as possible, so that the clamping force acts on the aluminum alloy workpiece. The clamping surface should be as close as possible to the machining surface, and the position where the force is not easy to cause deformation should be selected.
When the clamping force in several directions acts on the workpiece, the sequence of clamping should be considered. The clamping force should be applied first to make the workpiece contact the support, and should not be too large. For the main clamping force to balance the cutting force, It should be used in subsequent processes.
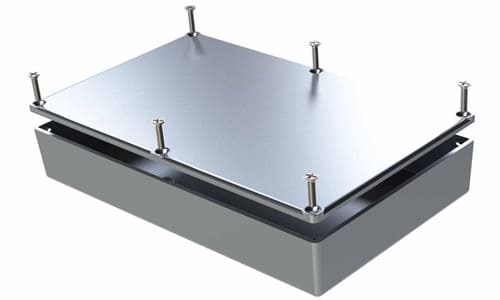
3. Deformation caused by the setting of parameters during machining of aluminum enclosures
During the cutting process of the aluminum alloy enclosure, due to the cutting force, the elastic deformation corresponding to the direction of the force is generated, which is cutter relieving we often say in the machining industry. Corresponding measures should be taken in machining parameters and tool selection to deal with such deformation. The tool is required to be sharp during finishing. On the one hand, it can reduce the resistance formed by the friction between the tool and the workpiece, and on the other hand, it can improve the heat dissipation effect of the tool when cutting the workpiece. , thereby reducing the possibility of deformation of aluminum alloy parts.
When CNC milling the large surface of the aluminum thin-walled enclosure, the single-edge milling method is used, and the tool parameters use a larger entering angle and a larger rake angle, the purpose is to reduce the cutting resistance.
Because this kind of cutting tool cuts “lightly and quickly”, it can reduce the deformation of thin-walled aluminum parts and is widely used in production.
In the machining of thin-walled aluminum enclosures, a reasonable tool angle is crucial to the magnitude of the cutting force during machining, the thermal deformation generated during the process, and the microscopic quality of the workpiece surface.
Therefore, when machining aluminum alloy thin-walled enclosures, high-speed tools and carbide tools are generally used. Whether the tool can be correctly selected is the key to dealing with the deformation of aluminum enclosures.
In machining, the heat generated by the friction between the CNC machine tool and the workpiece will also deform the workpiece, so high-speed cutting is often selected. In high-speed machining, since the chips are removed in a relatively short time, most of the cutting heat is taken away by the chips, reducing the thermal deformation of the workpiece; secondly, when working in a high-speed machining center, due to the reduction of the softened part of the cutting layer material , It can also reduce the deformation of the aluminum enclosure machining, which is beneficial to ensure that the enclosure has the precise size, shape and size.
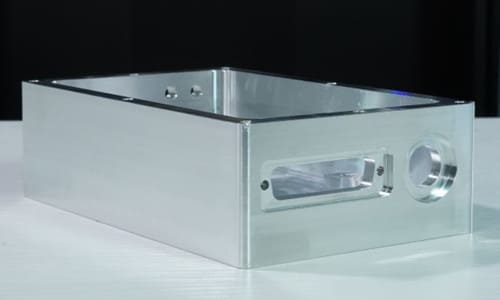
In addition, the cutting fluid of the CNC machining center is mainly used to reduce the friction and reduce the cutting temperature during the cutting process. Reasonable selection of cutting fluid plays an indispensable role in improving tool durability, surface quality and machining accuracy. Therefore, in order to prevent the deformation of aluminum alloy customized parts during machining, it is necessary to use a special cutting fluid with appropriate concentration. Using a reasonable cutting amount in the CNC machining process is an important part of ensuring the accuracy of the parts.
When machining thin-walled aluminum enclosures with high precision requirements, symmetrical machining is generally adopted to balance the stress generated on the opposite sides and achieve a relatively stable state, and the aluminum parts will be flat after machining.
However, when a large amount of cutting is adopted in a certain process, the workpiece will be deformed due to the unbalance of tensile stress and compressive stress. The deformation of the thin-walled aluminum enclosure during cutting on the machining center is multi-faceted. Some factors such as the clamping force when clamping the workpiece, the cutting force when cutting the workpiece, and the elastic deformation and plastic deformation generated when the workpiece hinders the cutting of the tool will make custom enclosure is deformed.
4. The deformation of the aluminum enclosures in the natural state after CNC machining is completed
After the aluminum enclosure is machined, there is internal stress in the machined part, and there is also deformation. To solve such a situation, some workpieces need to be divided into roughing and finishing, that is, after roughing is completed, aging treatment or heat treatment to remove stress, and then finishing.