When we get a drawing or sample, how to choose the suitable production process is an important work for engineer. Some parts can be made by Turning or milling, however some parts needs turning, milling or even more different processes to make.
The judgement of whether parts should be done by turning or milling depends on several factors such as the complexity of the part, the material used, the required precision and surface finish, and the production volume.
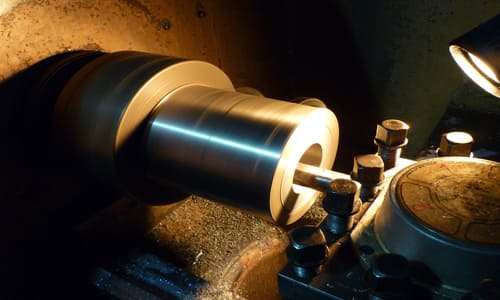
In general, turning is best suited for producing cylindrical parts, whereas milling is more effective for producing parts with complex shapes or features. Turning is also preferred when high surface finish and dimensional accuracy are required, while milling is better suited for roughing and removing larger amounts of material.
To determine which method is best for a specific part, it is important to consider the following factors:
Part geometry: If the part is cylindrical in shape or has circular features, turning is usually the preferred method. For parts with more complex shapes or features, milling may be a better choice.
Material: Certain materials, such as softer metals like aluminum, are better suited for milling, while harder materials like steel may be more efficiently turned.

Tolerance requirements: If tight tolerances are required, turning may be the better option as it can provide higher precision and accuracy than milling.
Surface finish: Turning is typically better for achieving a smoother surface finish, while milling is more effective for creating textured or patterned surfaces.
Production volume: For low-volume production runs, turning is usually more cost-effective, while milling may be more efficient for high-volume production.
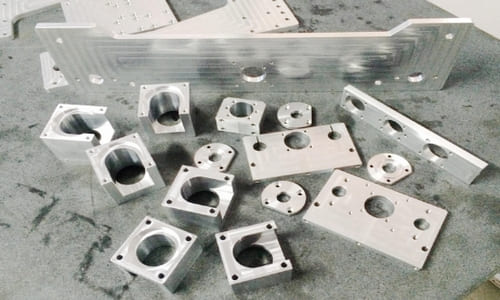
Ultimately, the best way to determine whether to use turning or milling for a specific part is to consult with a machining engineers who can evaluate the part’s requirements and recommend the best approach.