When it comes to CNC machining, three of the most common processes—CNC drilling, CNC milling, and CNC turning—are frequently used to create precision components. While they all involve machining materials with computer-controlled tools, each process serves a unique purpose and is best suited for specific applications. In this blog, we’ll break down the differences between these three processes, helping you choose the right method for your project.
1. What is CNC Drilling?
CNC drilling is a machining process designed to create precise, straight holes in a material. A rotating drill bit is used to penetrate the workpiece, forming cylindrical holes that may be used for assembly, threading, or fastener insertion.
Key features of CNC drilling include:
- Purpose: Hole creation (e.g., bolt holes, fluid passageways).
- Tools Used: Drill bits of varying sizes and shapes, such as twist drills, spade drills, and step drills.
- Applications: Manufacturing flanges, pipes, brackets, and other parts requiring precise holes.
Drilling is most effective when high accuracy and consistency are required for holes that are uniform in diameter and depth.
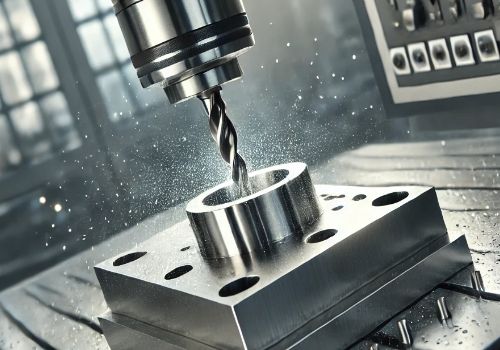
2. What is CNC Milling?
CNC milling is a more versatile process used to remove material from a workpiece by rotating cutting tools. Unlike drilling, milling can create complex shapes, slots, and contours in multiple axes.
Key features of CNC milling include:
- Purpose: Shaping, contouring, and slotting material.
- Tools Used: End mills, ball nose cutters, and face mills.
- Applications: Producing gears, housings, molds, and custom prototypes.
Milling machines can operate on 3, 4, or even 5 axes, allowing for highly complex geometries and greater flexibility than drilling.
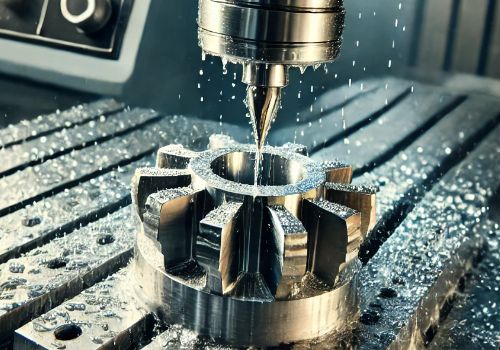
3. What is CNC Turning?
CNC turning is a machining process that shapes cylindrical or rotational parts by spinning the workpiece while a cutting tool removes material. This process is ideal for creating symmetrical parts.
Key features of CNC turning include:
- Purpose: Producing cylindrical or conical components.
- Tools Used: Lathe tools, grooving tools, and threading tools.
- Applications: Manufacturing shafts, bushings, and fasteners.
Turning machines, or lathes, excel at machining round components with tight tolerances and smooth surface finishes.
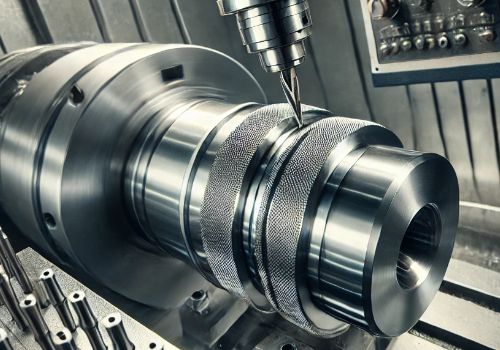
4. How CNC Drilling Differs from CNC Milling and Turning
Purpose and Functionality
- Drilling: Focuses solely on creating holes. It is specialized and straightforward.
- Milling: Handles a wide variety of tasks, such as cutting slots, shaping edges, and sculpting surfaces. It’s the most versatile process.
- Turning: Dedicated to shaping rotational parts by removing material from a spinning workpiece.
Tools and Movements
- Drilling: Uses a stationary tool to penetrate the workpiece. The movement is linear, usually along the Z-axis.
- Milling: Utilizes rotating tools that move along multiple axes (X, Y, Z) to cut material.
- Turning: The workpiece rotates while the cutting tool remains stationary or moves linearly.
Applications
- Drilling: Best for making holes with high precision and consistency.
- Milling: Ideal for complex, multi-surface machining tasks.
- Turning: Perfect for parts with symmetrical, cylindrical features.
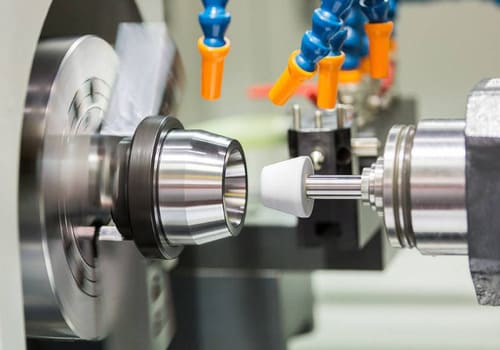
5. Choosing the Right Process for Your Needs
When deciding between CNC drilling, milling, and turning, consider the following:
- Material Shape:
- Use drilling for adding holes to flat or irregular surfaces.
- Opt for milling for intricate designs or when multiple features are needed on a single part.
- Choose turning if your part is cylindrical or rotational.
- Project Requirements:
- Precision Holes: Drilling is the go-to process.
- Complex Geometries: Milling is ideal for complex designs.
- Cylindrical Parts: Turning is unmatched for rotational symmetry.
- Production Volume:
- For high-volume, simple parts like bolts or bushings, turning may be more efficient.
- For low-volume, highly customized parts, milling offers versatility.
- Drilling is suitable for components requiring multiple uniform holes.
6. Integration of CNC Machining Processes
In many cases, manufacturers use a combination of these processes to achieve the desired results. For example, a part may first undergo turning to achieve its cylindrical shape, followed by drilling to add holes, and milling for additional contours.
7. Advantages of CNC Drilling, Milling, and Turning
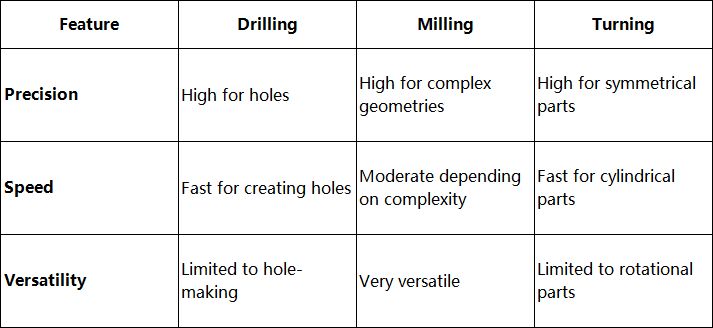
Conclusion
CNC drilling, milling, and turning are fundamental processes that cater to different machining needs. Understanding their unique functions, tools, and applications ensures that you choose the right process for your project, saving time and money while delivering high-quality results.
If you’re looking for a trusted partner to handle your CNC machining needs, domachining.com offers advanced solutions tailored to your specifications. From precise drilling to intricate milling and efficient turning, we deliver results that exceed expectations.
Contact us today to discuss your project and explore how CNC machining can help you achieve your manufacturing goals.