In the ever-evolving world of manufacturing, Artificial Intelligence (AI) is making a significant impact, especially in CNC (Computer Numerical Control) machining. By integrating AI into CNC machining processes, manufacturers are achieving unprecedented levels of efficiency, precision, and cost savings. But how exactly is AI transforming CNC machining, and what benefits does it bring? Let’s explore.
1. Enhancing Process Automation
AI enables CNC machines to operate with greater autonomy by using machine learning algorithms to analyze data and make decisions in real time. Traditional CNC machining requires precise programming and human supervision to ensure accuracy, but AI-powered systems can self-optimize.
For instance, AI-driven systems can automatically adjust cutting speeds, feed rates, and tool paths based on real-time feedback from sensors. This eliminates the need for constant operator intervention and ensures optimal performance without delays.
2. Predictive Maintenance for CNC Machines
Downtime is one of the biggest challenges in manufacturing. AI is revolutionizing maintenance through predictive analysis, allowing manufacturers to anticipate machine failures before they occur.
Sensors embedded in CNC machines collect data on vibrations, temperature, and tool wear. AI algorithms analyze this data to detect anomalies and predict when a machine might need servicing. This approach not only reduces downtime but also extends the lifespan of equipment by preventing catastrophic failures.
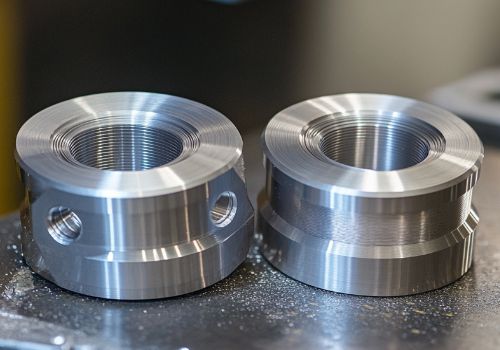
3. Improving Precision and Reducing Errors
One of the key benefits of AI in CNC machining is its ability to improve precision. AI-powered systems use advanced algorithms to learn from machining errors and adapt accordingly.
For example, AI can detect subtle inconsistencies in the machining process, such as deviations in tool paths or material deformation, and correct them in real-time. This ensures that parts meet tight tolerances and eliminates the need for extensive post-processing or rework.
4. Optimizing Tool Utilization
Tool wear is a significant factor in CNC machining costs. AI helps optimize tool usage by monitoring tool wear in real time and predicting when a tool needs to be replaced.
Additionally, AI can analyze machining data to recommend the most efficient cutting parameters, such as feed rates and spindle speeds, to maximize tool life. By reducing tool replacement frequency and ensuring optimal performance, AI helps manufacturers save both time and money.
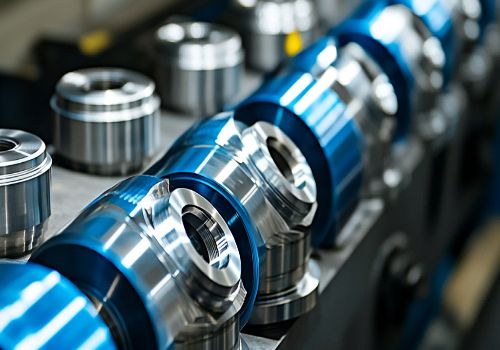
5. Reducing Material Waste
AI’s ability to optimize tool paths and machining parameters directly contributes to reducing material waste. By precisely calculating the most efficient cutting strategy, AI minimizes scrap material and ensures that raw materials are used effectively.
Furthermore, AI-driven simulations can predict how materials will behave during machining, enabling manufacturers to plan their processes more accurately and reduce trial-and-error waste.
6. Enhancing Quality Control
AI is playing a pivotal role in quality control for CNC machining. Vision-based AI systems can inspect machined parts for defects in real time, ensuring they meet strict quality standards.
These systems can identify surface imperfections, dimensional inaccuracies, or other defects with a level of precision that surpasses human inspection. This allows manufacturers to deliver consistent, high-quality products and reduce the risk of defective parts reaching customers.
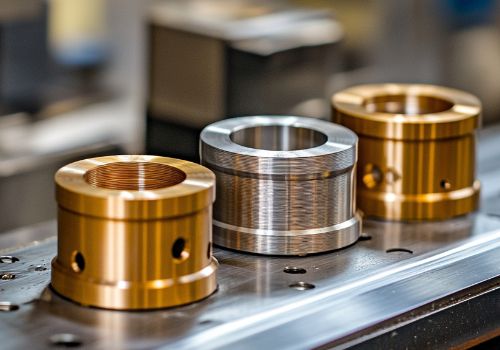
7. Streamlining Customization
In industries like aerospace, automotive, and medical devices, customization is often a necessity. AI makes customization more efficient by analyzing customer specifications and generating optimal machining programs automatically.
By reducing the time required to create custom CNC programs, AI helps manufacturers meet unique customer demands faster while maintaining high levels of accuracy and quality.
8. Real-Time Analytics and Data Utilization
AI enables manufacturers to harness the power of big data by analyzing machining operations in real time. Insights gained from this data can be used to:
- Identify bottlenecks in the production process.
- Optimize machining workflows.
- Improve machine performance over time.
With AI-driven analytics, manufacturers can make data-informed decisions to enhance productivity and reduce operational costs.
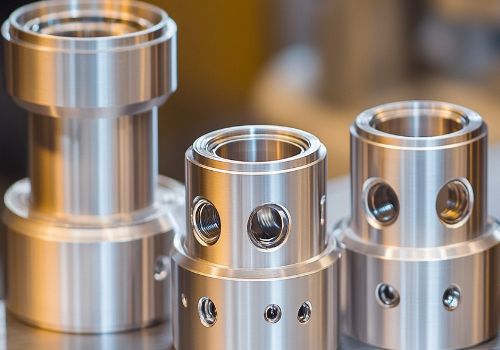
9. Applications in Multi-Axis CNC Machining
Multi-axis CNC machining involves complex tool movements, making it challenging to achieve precision without errors. AI algorithms excel in managing these complexities by predicting tool collisions, optimizing tool paths, and ensuring seamless coordination across multiple axes.
This is particularly valuable in industries requiring intricate designs, such as aerospace and medical device manufacturing.
Conclusion
Artificial Intelligence is revolutionizing CNC machining processes by improving automation, reducing errors, optimizing tool usage, and enhancing quality control. The integration of AI is not only boosting efficiency but also empowering manufacturers to achieve higher levels of precision, reduce costs, and minimize waste.
As the manufacturing industry continues to embrace Industry 4.0 technologies, the role of AI in CNC machining will only grow. Companies that invest in AI-powered CNC systems today will be well-positioned to stay competitive and meet the ever-increasing demands of modern manufacturing.
If you’re ready to take your CNC machining operations to the next level with AI, now is the time to act. Explore the possibilities and see how AI can transform your manufacturing processes.
About Us
At DO Machining, we specialize in cutting-edge CNC machining solutions that leverage AI and advanced technologies to deliver unmatched precision and quality. Contact us today to learn more about how we can optimize your manufacturing processes.