As the demand for high-precision and complex parts continues to rise across industries like aerospace, automotive, medical, and industrial equipment, advanced manufacturing technologies have become essential. One such breakthrough is 5-axis CNC machining, a technology that enables manufacturers to produce intricate components with unparalleled accuracy and efficiency.
In this blog, we’ll dive into what 5-axis machining is, how it works, its advantages, and its applications in manufacturing complex parts. If you’re looking for a solution to handle challenging geometries and tight tolerances, 5-axis machining might be the answer.
What Is 5-Axis Machining?
5-axis CNC machining is an advanced manufacturing process where the cutting tool moves along five different axes simultaneously. Unlike traditional 3-axis machining, where the cutting tool moves in the X, Y, and Z directions, 5-axis machining adds two rotational axes (A and B), allowing the tool to approach the workpiece from virtually any angle.
Key Features of 5-Axis Machining:
- Multidirectional Movement: Access to all angles of a workpiece without the need for repositioning.
- Enhanced Precision: Capable of achieving extremely tight tolerances, even for the most complex designs.
- Speed and Efficiency: Reduced setup times and faster production cycles for intricate components.
How 5-Axis Machining Benefits Complex Part Manufacturing
5-axis machining is the go-to technology for manufacturers dealing with intricate parts, whether they involve challenging geometries, tight tolerances, or demanding materials. Here’s why this technology excels in complex part production:
1. Precision and Accuracy
With 5-axis machining, manufacturers can achieve extraordinary levels of accuracy. This is crucial for industries like aerospace, where components such as turbine blades and structural parts must meet exact specifications to ensure safety and performance.
2. Reduced Setup Time
Traditional 3-axis machining often requires multiple setups to handle complex parts, increasing both time and the risk of errors. With 5-axis machining, multiple faces of a part can be machined in a single setup, improving both speed and consistency.
3. Versatility Across Materials
5-axis machines can work with a wide range of materials, including aluminum, titanium, steel, and composites. This makes them ideal for industries requiring high-strength, lightweight materials, such as automotive and medical manufacturing.
4. Cost Efficiency for Complex Parts
Although 5-axis machines are more advanced, they can reduce overall costs for complex parts by cutting down on labor, tooling, and setup time. This efficiency is especially beneficial for low to medium production runs.
5. Superior Surface Finish
The ability to machine intricate surfaces in one pass leads to a smoother finish. This is particularly important for parts like medical implants, where a flawless surface is critical for functionality and safety.
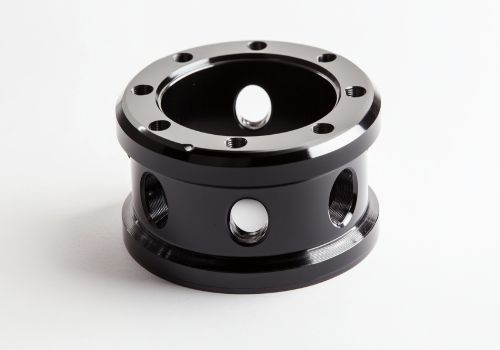
Applications of 5-Axis Machining in Complex Manufacturing
The versatility of 5-axis machining has made it indispensable for manufacturing high-precision, complex components across a variety of industries:
Aerospace Industry
The aerospace sector demands parts with complex geometries, lightweight materials, and impeccable accuracy. Examples include:
- Turbine Blades: Precision-crafted to handle high-stress environments.
- Structural Components: Designed for strength and weight optimization.
Automotive Industry
In automotive manufacturing, 5-axis machining is used to create high-performance components like:
- Engine Parts: Cylinder heads, pistons, and intake manifolds.
- Custom Parts: For racing and luxury vehicles, where precision and customization are paramount.
Medical Industry
Medical devices and implants often require intricate designs and biocompatible materials. Examples include:
- Prosthetic Implants: Customized for each patient’s anatomy.
- Surgical Instruments: Precision tools with complex features.
Industrial Equipment
For industrial machinery, 5-axis machining is used to create durable and precise parts, such as:
- Hydraulic Components: Complex valves and pump housings.
- Tooling: Custom molds and dies for manufacturing processes.
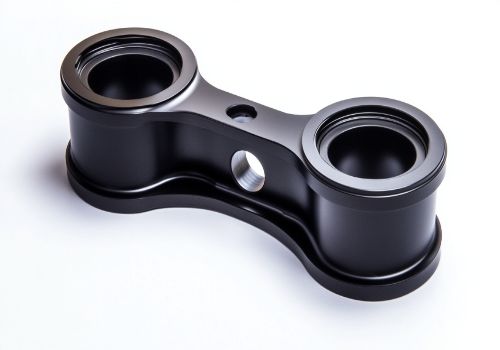
Choosing the Right 5-Axis Machining Service
Selecting the right machining provider can make all the difference in the success of your project. When evaluating a 5-axis CNC machining service, consider the following factors:
1. Experience with Complex Geometries
Look for a provider with a proven track record in high-precision machining for your specific industry.
2. Advanced Equipment
Ensure the machining service uses state-of-the-art 5-axis machines capable of meeting your specifications.
3. Material Expertise
Choose a provider experienced in working with the materials required for your project, whether it’s aluminum, titanium, or composites.
4. Quality Assurance
Certifications like ISO 9001 ensure that the provider adheres to strict quality control standards.
5. Custom Solutions
Every project is unique, so work with a provider that can offer tailored solutions to meet your specific needs.
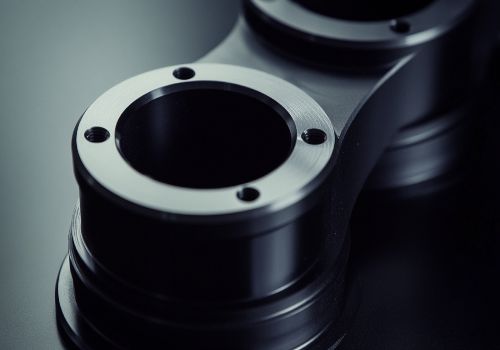
Conclusion: Unlocking the Potential of 5-Axis Machining
5-axis CNC machining is transforming the way manufacturers approach complex part production. Its ability to handle intricate geometries, reduce setup times, and deliver unmatched precision makes it an invaluable tool across industries.
Whether you’re designing aerospace components, automotive parts, or medical implants, partnering with an experienced 5-axis machining provider can help bring your vision to life with efficiency, precision, and quality.
Looking for a trusted partner for your 5-axis machining needs? At domachining.com, we specialize in high-precision manufacturing for complex parts across various industries. Contact us today for a free consultation or visit our website to learn more!