CNC (Computer Numerical Control) machining is a high-precision manufacturing process used in various industries, from aerospace and automotive to medical devices and consumer products. While CNC machining offers unparalleled accuracy, efficiency, and versatility, it’s essential to understand how to get the best price for these services without compromising quality. In this blog, we’ll explore several key factors that can help you optimize your CNC machining costs and achieve the best value for your money.
1. Choose the Right CNC Machining Company
The first step in getting the best price for CNC machining services is selecting the right company. While you may be tempted to go with the cheapest option, it’s important to balance cost with quality. Here are some factors to consider when evaluating CNC machining companies:
- Experience and Reputation: Look for a company with a strong track record and experience in your industry. An experienced company is less likely to make mistakes that lead to costly rework.
- Certifications: Ensure the company holds relevant certifications like ISO 9001 or industry-specific standards (e.g., AS9100 for aerospace, ISO 13485 for medical devices).
- Customer Reviews: Read customer reviews or ask for references to verify the company’s reliability, delivery times, and quality.
Why This Matters:
Choosing the right CNC machining company ensures that you get high-quality parts without unnecessary mistakes or delays, which can save you money in the long run.
2. Provide Clear and Accurate Designs
Providing a clear and accurate design for your CNC machining project is crucial for minimizing costs. Ambiguities in the design can lead to errors, revisions, and increased machining time, all of which contribute to higher costs.
Here’s what you can do to optimize your design for CNC machining:
- Use 3D CAD Models: 3D models are easier for machinists to interpret than 2D drawings. They reduce the chances of errors and make it easier for the CNC machining company to quote accurate prices.
- Specify Tolerances and Finishes: Be specific about the tolerances and surface finishes required for your parts. Tight tolerances and specialized finishes can increase machining time and complexity, which affects the overall price.
- Optimize for Manufacturability: Work with your design team to ensure the design is optimized for CNC machining. Avoid overly complex geometries that require more setup time or specialized tooling.
Why This Matters:
A well-prepared design reduces the need for rework and minimizes machining time, both of which help keep costs down.
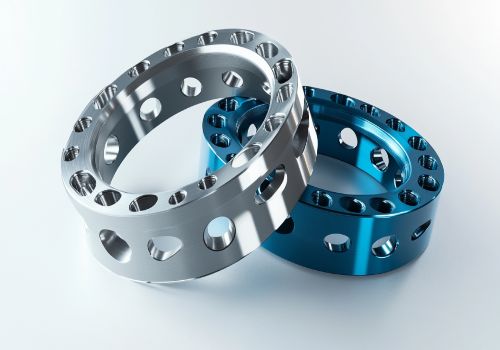
3. Understand the Material Costs
Material selection plays a significant role in the cost of CNC machining. The type of material you choose affects both the machining process and the final price. Some materials are more challenging to machine, requiring specialized tools or techniques, which can increase costs.
Here’s how to manage material costs effectively:
- Choose the Right Material: Different materials have different costs and machining characteristics. For example, aluminum is generally more affordable and easier to machine than stainless steel or titanium.
- Avoid Over-Specifying Materials: While certain applications require high-performance materials like titanium or Inconel, these materials are significantly more expensive. Consider whether a less expensive material can still meet your project’s requirements.
- Buy in Bulk: If you’re producing large volumes of parts, you may be able to negotiate a better material price by purchasing in bulk.
Why This Matters:
By selecting the right material and avoiding unnecessary upgrades, you can reduce the overall cost of CNC machining while still meeting your project’s specifications.
4. Optimize the Production Process
The way your project is produced can have a significant impact on the cost of CNC machining. The more efficient the production process, the less you will pay. Here are some ways to optimize the production process:
- Use Standard Tools and Techniques: Custom tools or specialized processes often cost more than standard, readily available tools. By designing parts that can be made using off-the-shelf tools, you can reduce costs.
- Consolidate Parts: If you’re producing multiple parts, consider consolidating them into a single part or combining operations to reduce the number of setups and machining cycles. This can help lower labor and machine time costs.
- Consider Batch Production: If you need to produce a large number of parts, batch production can be more cost-effective than one-off prototypes. The initial setup costs are higher, but the per-unit cost decreases as production volume increases.
Why This Matters:
Optimizing the production process reduces the overall machining time, which leads to cost savings. Fewer setups and less machine time mean lower costs.
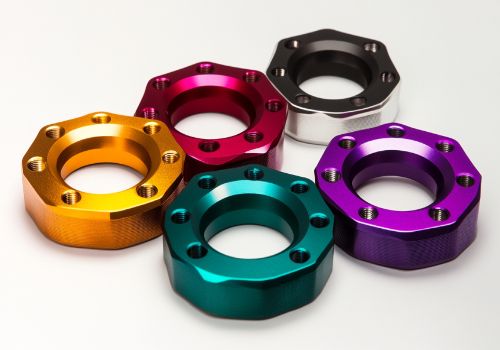
5. Request Quotes from Multiple CNC Machining Companies
Getting quotes from multiple CNC machining companies allows you to compare prices and find the best deal. However, it’s important to ensure that all quotes are based on the same specifications to make an accurate comparison. When requesting quotes, make sure to:
- Provide Detailed Specifications: Include material type, tolerances, finishes, and production volume in your quote request.
- Clarify Lead Time Expectations: Make sure you understand the lead times offered by different companies, as expedited services may come with a premium.
- Ask About Hidden Costs: Some CNC machining companies may charge extra for services such as tooling setup or post-processing. Be sure to ask about any potential hidden fees upfront.
Why This Matters:
Getting multiple quotes ensures you’re getting the best value for your CNC machining project. It allows you to compare pricing, lead times, and service offerings to make an informed decision.
6. Leverage Technology for Efficiency
Many CNC machining companies now incorporate cutting-edge technology, such as automation, AI, and advanced CAD/CAM systems, to improve efficiency and reduce costs. By choosing a company that embraces these technologies, you can benefit from faster turnaround times and more accurate machining, all of which contribute to cost savings.
- Automation: Automated systems can reduce the need for manual labor, speeding up production and reducing costs.
- AI-Driven Process Optimization: AI algorithms can optimize machine settings, predict maintenance needs, and reduce errors, leading to lower costs.
Why This Matters:
Leveraging advanced technology ensures that your project is completed as efficiently and accurately as possible, which leads to cost savings and improved overall value.
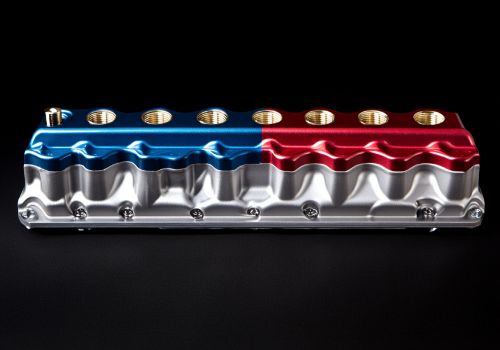
7. Minimize Post-Processing Costs
Post-processing, such as deburring, polishing, or coating, can add to the final cost of CNC machining. While some post-processing is necessary for specific applications, try to design parts that require minimal additional steps after machining.
- Design for Minimal Finishing: Simplify your designs to avoid complicated post-processing.
- Pre-Select Finishing Options: Choose from standard finishes that are cost-effective and commonly used in the industry.
Why This Matters:
Minimizing post-processing reduces additional costs and speeds up the overall production time, resulting in a lower final price.
Conclusion
Getting the best price for CNC machining services requires a combination of selecting the right machining company, optimizing your design and material choices, and understanding the production process. By taking these steps, you can ensure you’re getting the most value out of your investment while maintaining the quality and precision that CNC machining is known for.
At domachining.com, we specialize in providing cost-effective, high-quality CNC machining services tailored to your specific needs. Contact us today to learn how we can help you get the best price for your CNC machining project!