When sourcing CNC machined parts, quality is paramount. Poorly manufactured components can lead to production delays, increased costs, and subpar end products. Selecting the right supplier and implementing best practices can help you consistently receive high-quality CNC machined parts. In this blog, we’ll share practical tips to ensure you get the precision and performance you need from your CNC machining supplier.
1. Select a Reputable CNC Machining Supplier
The foundation of receiving high-quality CNC machined parts is choosing a supplier with a proven track record. Here are some factors to consider when evaluating potential suppliers:
- Certifications: Look for suppliers with certifications such as ISO 9001, which demonstrates their commitment to quality management.
- Experience: Opt for a supplier with extensive experience in your industry and with the materials and designs you require.
- Customer Reviews: Research online reviews or request references to learn about the supplier’s performance and reliability.
- Equipment: Ensure the supplier uses advanced CNC machines and the latest technology for precision manufacturing.
Why It Matters:
A reliable supplier minimizes the risk of defects and delays, ensuring your projects stay on schedule and within budget.
2. Define Clear Specifications
One of the most critical steps in ensuring high-quality parts is providing detailed and accurate specifications. Ambiguities in your design can lead to errors and inconsistencies. Be sure to include:
- Material Type: Specify the exact material required, such as aluminum, stainless steel, or plastic, and provide any relevant material grades.
- Dimensions and Tolerances: Clearly define all dimensions and tolerances to ensure parts meet your exact requirements.
- Surface Finish: Include details about the desired surface finish, such as anodizing, powder coating, or polishing.
- Application Requirements: Share information about how the part will be used, including load capacity, environmental conditions, and performance expectations.
Why It Matters:
Detailed specifications reduce miscommunication and ensure the supplier understands your requirements, leading to fewer mistakes.
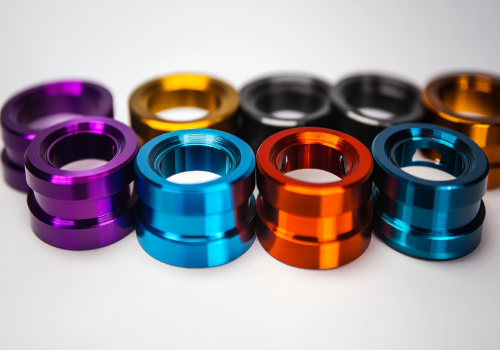
3. Inspect Sample Parts
Before committing to full production, request prototype or sample parts from your supplier. This allows you to:
- Evaluate Quality: Inspect the sample parts for accuracy, surface finish, and functionality.
- Verify Tolerances: Use measurement tools such as calipers or coordinate measuring machines (CMM) to confirm the parts meet your tolerances.
- Test Performance: If possible, test the parts under real-world conditions to ensure they meet your application’s requirements.
Why It Matters:
Inspecting samples helps you identify any issues early in the process, reducing the likelihood of costly revisions or rejected batches later on.
4. Establish a Quality Control Process
Work with your supplier to implement a robust quality control (QC) process. This may include:
- In-Process Inspections: Request that the supplier performs inspections during production to catch errors early.
- Final Inspection Reports: Ask for detailed inspection reports, including measurements and test results, for each batch of parts.
- Third-Party Verification: Consider hiring a third-party inspection service for additional quality assurance.
Why It Matters:
A strong QC process ensures that defects are identified and corrected before parts are shipped, saving time and money.
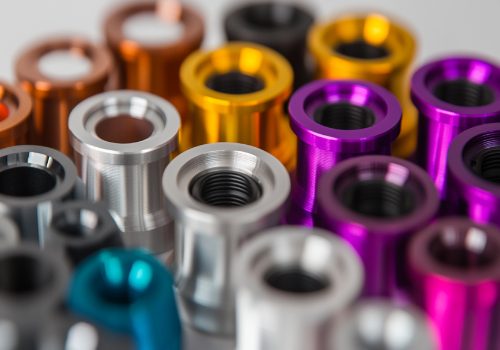
5. Communicate Regularly with Your Supplier
Open and consistent communication with your CNC machining supplier is essential for maintaining quality.
- Regular Updates: Request updates on production progress and any potential challenges.
- Feedback Loop: Provide feedback on delivered parts to help the supplier improve future production runs.
- Collaborative Problem-Solving: Work together to address any quality issues or design adjustments.
Why It Matters:
Strong communication builds trust and ensures both parties are aligned on expectations and goals.
6. Leverage Technology for Precision
Many modern CNC machining suppliers use advanced technology to enhance precision and quality. Ask your supplier about their use of:
- CAD/CAM Software: Ensures accurate design-to-production translation.
- 5-Axis CNC Machines: Allows for greater precision and flexibility in complex geometries.
- Quality Monitoring Systems: Uses sensors and software to detect errors in real time during production.
Why It Matters:
Suppliers who embrace advanced technology are better equipped to deliver high-quality parts consistently.
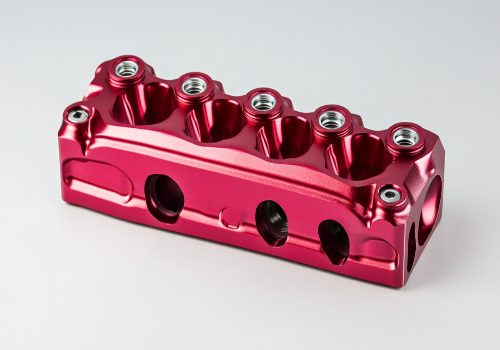
7. Request Certifications and Documentation
High-quality suppliers often provide certifications and documentation to verify the quality of their materials and processes. Common documents include:
- Material Certificates: Confirms the material grade and origin.
- Inspection Reports: Details measurements and tolerances for the batch.
- Compliance Certifications: Verifies compliance with industry standards, such as RoHS or FDA requirements.
Why It Matters:
Documentation provides transparency and reassurance that the parts meet your exact requirements.
8. Build a Long-Term Partnership
Establishing a long-term relationship with your CNC machining supplier can improve quality and streamline future projects.
- Supplier Familiarity: A long-term supplier becomes more familiar with your needs and expectations, leading to fewer errors.
- Preferred Customer Status: Loyal customers may receive priority service, faster lead times, and better pricing.
- Continuous Improvement: Collaborating over time allows for ongoing process improvements.
Why It Matters:
A strong partnership fosters trust, reliability, and improved outcomes for both parties.
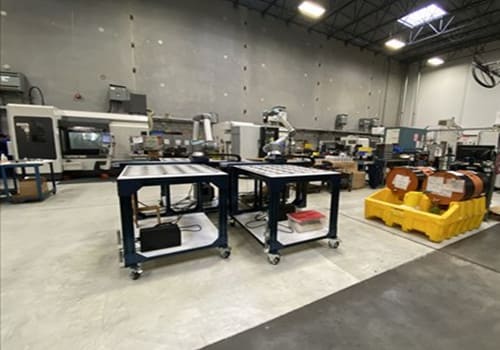
Conclusion
Ensuring high-quality CNC machined parts requires careful planning, clear communication, and a strong partnership with your supplier. By following the tips outlined in this blog, you can minimize risks, reduce costs, and consistently receive parts that meet your exact specifications.
At domachining.com, we pride ourselves on delivering top-quality CNC machining services backed by state-of-the-art technology, rigorous quality control, and exceptional customer service. Contact us today to learn how we can meet your CNC machining needs with precision and reliability.