Sourcing CNC machining services is a critical step in manufacturing precision parts. However, many businesses encounter costly mistakes that lead to delays, quality issues, and unnecessary expenses. Whether you’re ordering prototypes, small batches, or large-scale production, avoiding these common pitfalls can save time, money, and headaches.
In this blog, we’ll cover the most common mistakes when sourcing CNC machining services and how you can avoid them to ensure smooth and cost-effective production.
1. Failing to Define Clear Requirements
One of the biggest mistakes companies make is not providing detailed specifications to the CNC machining supplier. Without clear requirements, manufacturers may misinterpret your needs, leading to incorrect parts, costly revisions, or delays.
How to Avoid This Mistake:
✔ Provide precise drawings with exact measurements, tolerances, and material requirements.
✔ Use standard CAD file formats like STEP, IGES, or STL to ensure compatibility.
✔ Clearly state surface finishes, coatings, and post-processing requirements.
✔ Communicate expected quality control (QC) standards, such as ISO 9001 or AS9100 certification.
Why It Matters:
A well-defined project scope reduces miscommunication, minimizes errors, and ensures your CNC machining supplier delivers parts exactly as required.
2. Choosing the Wrong CNC Machining Supplier
Not all CNC machining companies offer the same level of expertise, technology, or customer service. Selecting the wrong supplier can lead to low-quality parts, missed deadlines, and poor communication.
How to Avoid This Mistake:
✔ Research suppliers with a strong industry reputation, positive customer reviews, and proven expertise in CNC machining.
✔ Verify their capabilities, including 3-axis, 4-axis, and 5-axis CNC machining, material options, and surface treatments.
✔ Request samples or case studies to evaluate their work quality.
✔ Ask about lead times and on-time delivery rates.
Why It Matters:
A reliable CNC machining supplier ensures consistent quality, meets deadlines, and provides expert guidance to optimize your designs.
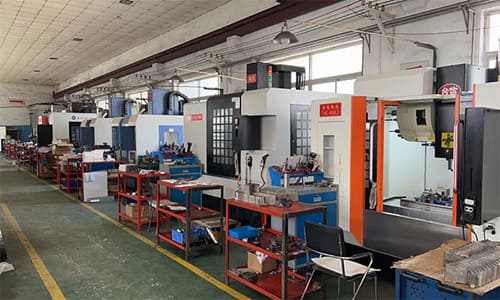
3. Prioritizing Cost Over Quality
While it’s important to stay within budget, choosing the cheapest CNC machining service can be a costly mistake in the long run. Low-cost suppliers may cut corners by using substandard materials, outdated machinery, or poor quality control.
How to Avoid This Mistake:
✔ Compare quotes carefully, considering material quality, precision, and additional costs like finishing and inspection.
✔ Check if the supplier follows international quality standards (ISO 9001, ISO 13485, or AS9100 for aerospace parts).
✔ Consider the total cost of ownership—cheaper parts that fail may cost more due to rework, downtime, and lost revenue.
Why It Matters:
High-quality CNC machining reduces the risk of defective parts, ensures durability, and enhances performance, making it a better long-term investment.
4. Overlooking Material Selection
Selecting the wrong material for CNC machining can lead to structural failures, increased costs, and machining inefficiencies. Some materials are harder to machine, while others may not withstand certain environmental conditions.
How to Avoid This Mistake:
✔ Consult your CNC supplier to choose the best material based on strength, weight, corrosion resistance, and cost.
✔ Consider the machinability of materials like aluminum, stainless steel, titanium, and plastics.
✔ Request material certifications to verify quality and compliance with industry standards.
Why It Matters:
Proper material selection ensures optimal performance, cost efficiency, and durability of the final product.
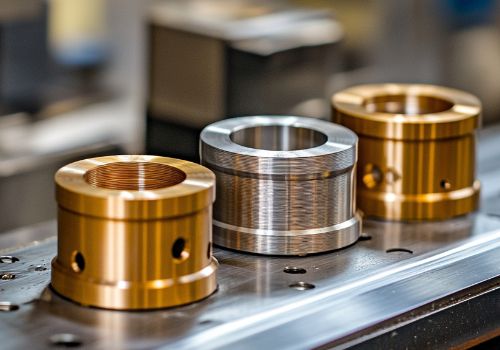
5. Ignoring Tolerance Requirements
Many businesses overlook tolerance specifications, assuming standard machining precision is enough. However, if tolerances are too tight, costs may increase significantly due to extra machining time and higher rejection rates.
How to Avoid This Mistake:
✔ Define realistic tolerances based on the part’s function—don’t specify ultra-tight tolerances unless necessary.
✔ Consult with your CNC machining partner about cost-effective tolerance ranges for your design.
✔ Use Geometric Dimensioning & Tolerancing (GD&T) for accurate and consistent measurements.
Why It Matters:
Properly defined tolerances balance cost and precision, ensuring your part functions as intended without unnecessary expenses.
6. Not Requesting Prototypes or Small Batch Runs
Skipping prototype testing or small production runs can lead to major quality issues in full-scale manufacturing, resulting in wasted resources and costly rework.
How to Avoid This Mistake:
✔ Start with a prototyping phase to verify design feasibility and functionality.
✔ Order small batches to test parts before committing to large-scale production.
✔ Work closely with the CNC supplier to identify and resolve design or machining issues early.
Why It Matters:
Prototyping helps detect potential design flaws, fitment issues, or performance concerns, saving time and money in the long run.
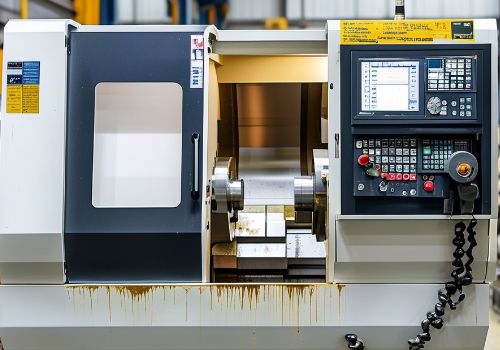
7. Underestimating Lead Times
Delays in CNC machining can disrupt supply chains and production schedules. Many companies fail to account for material procurement, machining complexity, and finishing processes, resulting in missed deadlines.
How to Avoid This Mistake:
✔ Discuss realistic lead times with your CNC machining supplier before placing an order.
✔ Factor in machining time, post-processing, quality inspections, and shipping.
✔ Plan for unexpected delays by ordering parts in advance or maintaining safety stock.
Why It Matters:
Understanding lead times allows you to better manage inventory, prevent production halts, and meet project deadlines.
8. Lack of Clear Communication with the Supplier
Miscommunication can lead to incorrect parts, increased costs, and production delays. If you don’t provide clear and ongoing feedback, your supplier may not fully understand your requirements.
How to Avoid This Mistake:
✔ Establish a direct point of contact with your CNC machining provider for seamless communication.
✔ Use email, video calls, and collaborative platforms to track progress.
✔ Request regular updates, inspection reports, and sample approvals before mass production.
Why It Matters:
Effective communication ensures fewer misunderstandings, better quality control, and smoother production workflows.
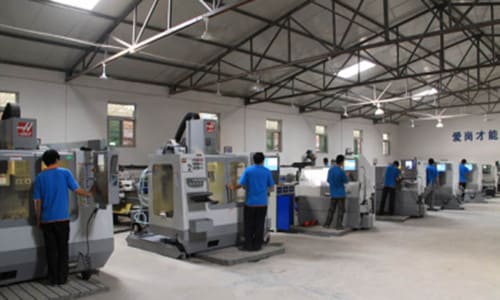
9. Ignoring Post-Processing and Surface Finishing
Many businesses overlook post-processing requirements, leading to parts that don’t meet aesthetic, functional, or durability standards.
How to Avoid This Mistake:
✔ Clearly define surface finishing needs, such as anodizing, powder coating, polishing, or heat treatment.
✔ Ask the supplier if they provide in-house finishing or outsource it to third-party vendors.
✔ Ensure post-processing doesn’t alter part dimensions beyond acceptable tolerances.
Why It Matters:
The right surface finish improves durability, corrosion resistance, and overall product appearance, making it essential for high-quality parts.
Conclusion
Sourcing CNC machining services requires careful planning and due diligence. By avoiding these common mistakes—unclear specifications, choosing the cheapest supplier, overlooking tolerances, or neglecting communication—you can ensure high-quality parts, cost efficiency, and smooth production processes.
At domachining.com, we specialize in high-precision CNC machining with a focus on quality, accuracy, and timely delivery. Contact us today to discuss your project and get a quote!