CNC machining is one of the most precise and reliable manufacturing methods, but without careful design planning, costs can rise, and efficiency can suffer. By optimizing your CNC machining design, you can reduce production time, minimize material waste, and lower overall costs. Here are some practical tips to enhance your CNC machining design for cost-effectiveness and efficiency.
1. Choose the Right Material Wisely
Material selection plays a crucial role in cost and efficiency. While metals like aluminum and stainless steel are common choices, their machinability differs.
- Aluminum: Excellent machinability, lightweight, and cost-effective.
- Stainless Steel: Strong and corrosion-resistant but harder to machine.
- Plastics (ABS, POM, Nylon): Easier to machine and cost-effective for non-load-bearing parts.
- Titanium: Durable but expensive and difficult to machine.
Choosing materials that are easy to machine can significantly reduce machining time and tool wear, improving efficiency.
2. Simplify Your Design
Complex geometries and unnecessary features increase machining time and costs. When designing for CNC machining:
- Avoid intricate internal corners that require small-diameter tools and longer machining cycles.
- Minimize thin walls, as they can vibrate and require slower machining speeds.
- Use standard hole sizes to avoid the need for custom tooling.
A streamlined design ensures faster machining and reduces the likelihood of errors.
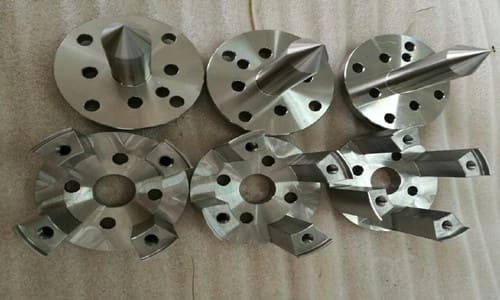
3. Optimize Tolerances
While tight tolerances ensure precision, they also increase costs. Not every part of your design requires ultra-tight tolerances.
- Standard Tolerance: ±0.1mm is usually sufficient for non-critical features.
- Tight Tolerance: Use only for critical dimensions that affect part functionality.
Relaxing tolerances where possible reduces machining complexity and tool wear, ultimately lowering costs.
4. Design for Efficient Toolpaths
The more tool changes and repositioning required, the longer the machining time. To improve efficiency:
- Minimize setup changes by designing parts that can be machined in a single setup.
- Avoid deep pockets that require long-reach tools, which slow down machining.
- Use fillets (rounded corners) instead of sharp internal corners to allow for faster machining with larger tools.
Efficient toolpaths lead to reduced production time and lower machining costs.
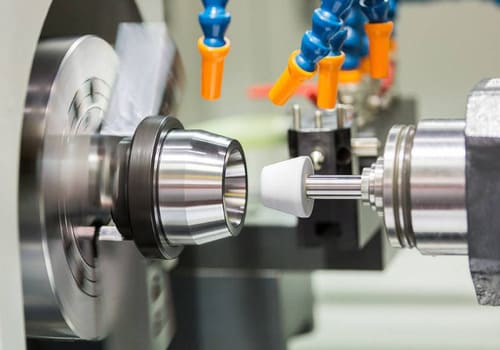
5. Reduce Excessive Material Removal
Removing large amounts of material increases machining time and tool wear. Instead:
- Use near-net-shape raw materials to minimize waste.
- Consider hollowing out non-essential areas to save material.
- If possible, use extrusions or pre-formed stock that match your design dimensions closely.
By reducing unnecessary material removal, you can decrease costs and improve production speed.
6. Optimize Threading and Fastener Selection
Threads and fasteners can affect both cost and ease of machining.
- Use standard thread sizes to avoid additional tooling costs.
- Limit deep threads, as they require multiple passes and increase machining time.
- Consider press-fit or snap-fit designs for plastic components to reduce fastener requirements.
Selecting the right threading approach helps keep costs manageable while ensuring part functionality.
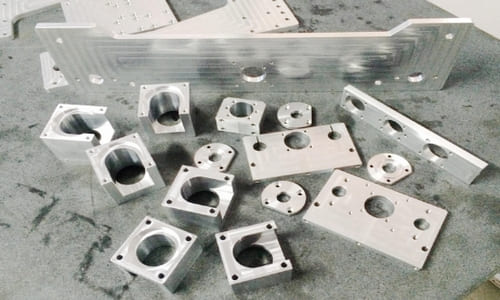
7. Minimize Surface Finishing Requirements
Additional finishing processes like anodizing, polishing, or powder coating add to the cost and lead time.
- Use materials that have a naturally good finish to minimize post-processing.
- Specify surface finishes only where necessary to reduce processing costs.
- Choose a consistent finish requirement across all parts to streamline production.
Minimizing finishing requirements speeds up production and lowers overall costs.
8. Work with an Experienced CNC Machining Partner
Partnering with an experienced CNC machining supplier can help you optimize your design for cost and efficiency. They can:
- Recommend design modifications to improve machinability.
- Suggest cost-effective material alternatives.
- Provide insight into the latest machining technologies that can reduce costs.
Early collaboration with your CNC manufacturer ensures that your design is optimized for production from the start.
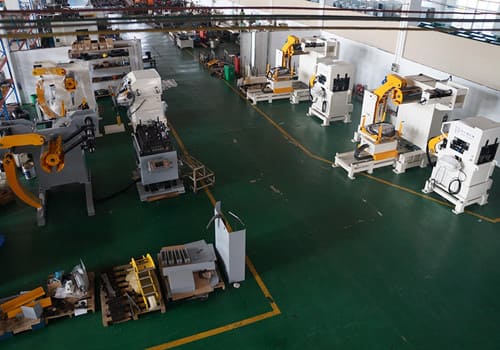
Conclusion
Optimizing your CNC machining design is essential for reducing costs, improving efficiency, and ensuring high-quality results. By choosing the right materials, simplifying designs, optimizing tolerances, and reducing unnecessary machining steps, you can achieve cost-effective and efficient production.
Looking for a reliable CNC machining partner to help you optimize your designs? DO Machining specializes in precision machining solutions tailored to your needs. Contact us today for expert advice and a free quote!