When it comes to CNC machining, material costs can account for a significant portion of your total project expense. That’s why improving material yield—the amount of usable material extracted from raw stock—is a key factor in boosting profitability and sustainability.
In this blog, we’ll share actionable tips on how to maximize material usage, minimize waste, and ultimately save money in CNC machining without compromising on quality.
1. Optimize Your Part Layout and Nesting
Efficient part layout is essential for improving material yield. In CNC milling or laser cutting, smart nesting can drastically reduce leftover material.
✅ Pro Tips:
-
Use CAD/CAM software to nest parts tightly
-
Rotate parts for optimal fit on raw stock
-
Align similar parts for shared cutting paths
The goal is to get as many usable parts as possible out of each raw material sheet, block, or bar.
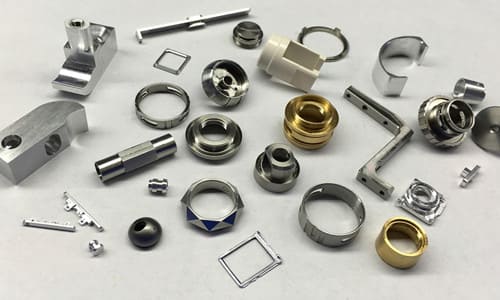
2. Choose the Right Material Dimensions
Ordering material that closely matches your part size helps minimize machining time and scrap. Oversized stock might seem safer, but it leads to more material waste.
💡 Tip:
Work with your supplier to source pre-cut blanks or custom-sized materials that match your design specs. You’ll reduce waste and lower your overall cost.
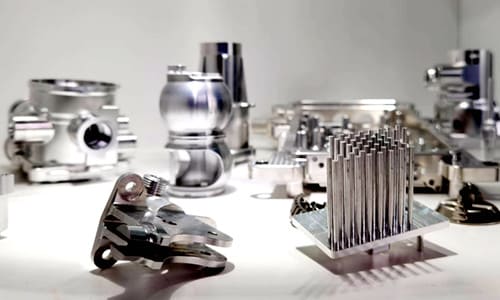
3. Avoid Over-Engineering Your Designs
Designs with excessive material volume or unnecessarily tight tolerances often lead to higher waste. Sometimes, a simple redesign can increase yield without affecting part performance.
🎯 Ask Yourself:
-
Can any non-functional areas be hollowed out?
-
Are all features essential?
-
Are tolerances too strict?
Design for function and manufacturability, not overkill.
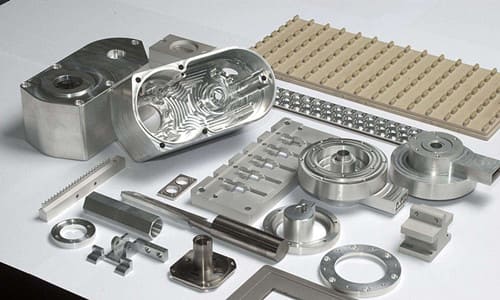
4. Use Simulation and CAM Tools Effectively
Advanced CAM (Computer-Aided Manufacturing) software allows you to simulate machining operations before cutting begins. This helps identify potential waste areas and optimize tool paths.
📊 CAM Benefits:
-
Simulate stock removal visually
-
Adjust cutting strategy for minimal waste
-
Calculate remaining material for future use
Simulation helps you plan for better stock utilization from the start.
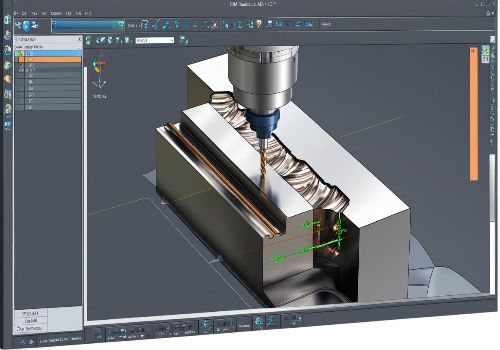
5. Reuse and Recycle Offcuts
Don’t discard every offcut! Depending on the material and shape, many leftover pieces can be repurposed for smaller parts, prototypes, or fixture blocks.
Work with a machining partner who tracks and manages usable scrap inventory to further improve material yield.
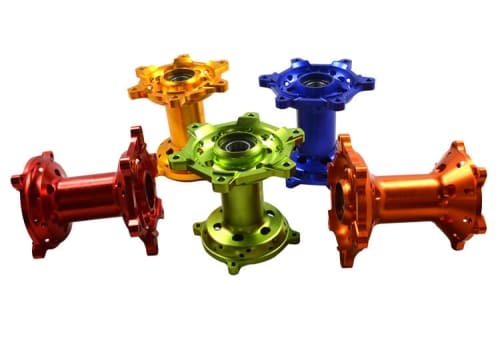
6. Standardize Part Sizes Across Projects
If you frequently produce similar parts, try to standardize dimensions wherever possible. This simplifies sourcing, reduces offcut waste, and enables bulk material use more efficiently.
The more modular your parts, the easier it is to achieve better material yield across multiple jobs.
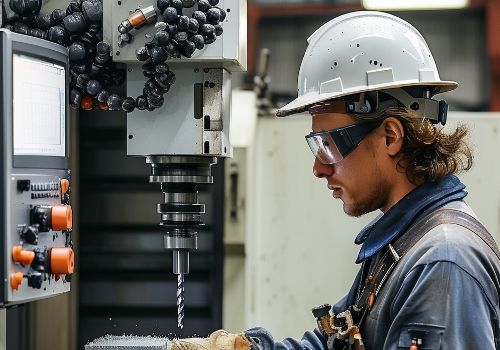
7. Partner With a Machining Company That Prioritizes Efficiency
The right CNC machining service provider will not only deliver precision—but also offer design feedback, suggest better material options, and ensure minimal waste production.
At DO Machining, we use advanced simulation software and lean manufacturing processes to help our customers maximize material utilization and reduce costs.
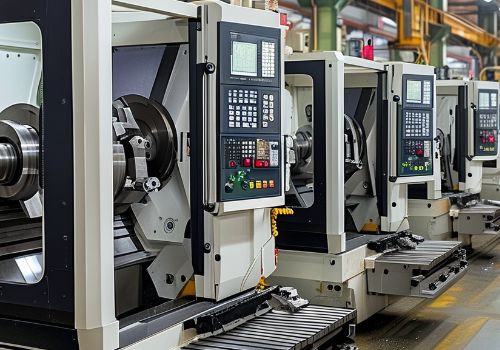
Conclusion
Improving material yield is not just about reducing waste—it’s about smart engineering, smart design, and smart manufacturing. By following the strategies above, you’ll save money, improve efficiency, and reduce your environmental footprint.
Ready to optimize your next CNC project? Contact DO Machining for professional support, from design to delivery.
👉 Learn more at: https://www.domachining.com