CNC machining has revolutionized the way manufacturers create precise and reliable components. While metals often dominate discussions about CNC machining, plastics are an equally important material in many industries. This blog will explore why plastics are a valuable choice for CNC machining, their benefits, common applications, and the factors to consider when machining plastic components.
1. Why Choose Plastics for CNC Machining?
Plastics offer a range of unique properties that make them a preferred choice for various applications:
- Lightweight: Plastics are significantly lighter than metals, making them ideal for weight-sensitive applications.
- Cost-Effective: Many plastics are more affordable than metals, reducing overall production costs.
- Corrosion Resistance: Unlike metals, plastics do not corrode, making them suitable for harsh environments.
- Electrical Insulation: Plastics are excellent insulators, widely used in electronics and electrical applications.
- Versatility: Plastics come in numerous types, each with specific properties tailored to different applications.
2. Benefits of CNC Machining for Plastics
Precision and Accuracy
CNC machining ensures tight tolerances and detailed geometries, even with challenging plastic materials.
Reduced Waste
CNC machining is highly efficient, minimizing material waste during the production process.
Wide Material Compatibility
From ABS and polycarbonate to PTFE and acrylic, CNC machining accommodates a broad range of plastics.
Fast Prototyping and Production
CNC machining accelerates the production of prototypes and small to medium production runs.
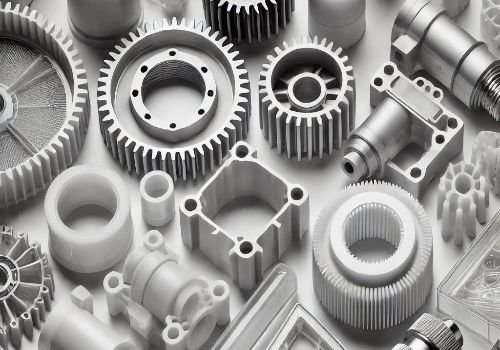
3. Types of Plastics Used in CNC Machining
Acrylic (PMMA)
- Known for transparency and resistance to impact.
- Ideal for optical components like lenses and screens.
Polycarbonate (PC)
- Highly durable and impact-resistant.
- Common in safety equipment and automotive parts.
ABS (Acrylonitrile Butadiene Styrene)
- Lightweight and cost-effective.
- Frequently used in consumer goods and enclosures.
PTFE (Teflon)
- Offers excellent heat resistance and low friction.
- Widely used in sealing and chemical applications.
Nylon
- Strong, lightweight, and wear-resistant.
- Common in gears, bearings, and industrial components.
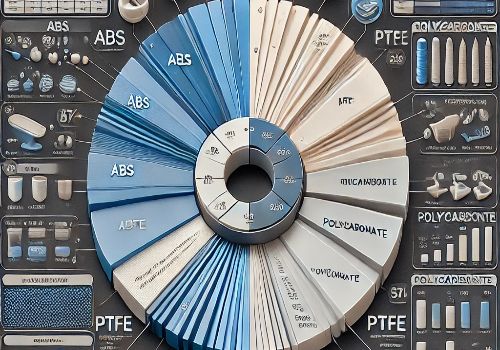
4. Challenges of CNC Machining Plastics
Thermal Deformation
Plastics can deform under heat, requiring careful tool selection and cutting speeds.
Surface Finish
Achieving a smooth finish on plastics may require additional post-processing.
Material Variability
Different plastics exhibit unique properties, requiring tailored machining strategies.
5. Applications of CNC Machined Plastic Components
Electronics
Used for housings, connectors, and insulating components.
Automotive
Ideal for lightweight parts like dashboards, handles, and under-hood components.
Medical Devices
CNC-machined plastics are used for surgical instruments, implants, and diagnostic equipment.
Aerospace
Lightweight plastic components are essential for fuel efficiency and durability in aerospace applications.
Consumer Products
Used in everything from household appliances to sporting goods.
6. Factors to Consider for CNC Plastic Machining
- Material Selection: Choose the right plastic based on application requirements.
- Tooling: Use sharp, appropriate tools to avoid material deformation.
- Cooling: Implement proper cooling systems to manage heat generation.
- Tolerances: Adjust machining parameters to meet the required tolerances.
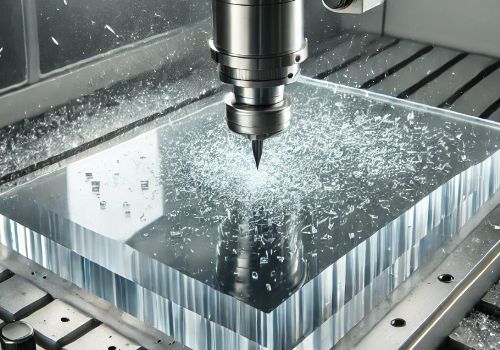
7. Conclusion
CNC machining for plastics opens up endless possibilities for innovation across industries. With the right material selection and machining techniques, manufacturers can create high-quality plastic components tailored to their needs.
At domachining.com, we specialize in CNC machining for both metals and plastics, offering precision solutions to meet diverse industry demands. Contact us today to learn more about how we can help with your next project!