As an expert in the CNC machining industry, I foresee several pivotal trends shaping the global CNC machining market in 2025. These trends align with ongoing technological advancements, economic shifts, and emerging demands across key industries like automotive, aerospace, and electronics.
Key Development Trends for 2025
1. Integration of Artificial Intelligence (AI) and Machine Learning (ML)
- AI-driven CNC systems will enhance precision by learning from previous machining operations, optimizing cutting paths, and predicting tool wear more accurately.
- ML algorithms will improve predictive maintenance capabilities, minimizing downtime and extending equipment lifespan.
2. Expansion of Hybrid Manufacturing
- The combination of CNC machining and additive manufacturing will continue to grow. This hybrid approach enables the creation of complex parts with reduced material waste, particularly benefiting aerospace and medical industries.
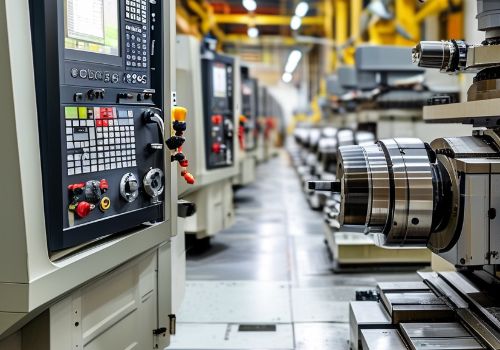
3. Sustainability as a Core Strategy
- Manufacturers will prioritize eco-friendly practices, including the use of recyclable materials and energy-efficient machines. CNC machining processes will adopt closed-loop systems to minimize waste.
- The push for net-zero emissions will lead to innovations in energy-saving technologies and green materials.
4. Advanced Automation and Robotics
- Collaborative robots (cobots) will become more prevalent in smaller workshops, while fully automated machining cells will dominate large-scale production.
- Automation will extend beyond machining to include material handling, inspection, and finishing processes, significantly reducing human intervention and cycle times.
5. IoT and Smart Factories
- Real-time monitoring via IoT-enabled CNC machines will offer actionable insights into machine performance, allowing for on-the-fly adjustments to improve efficiency.
- Cloud computing and digital twins will support remote management and simulation, enabling smarter production decisions.
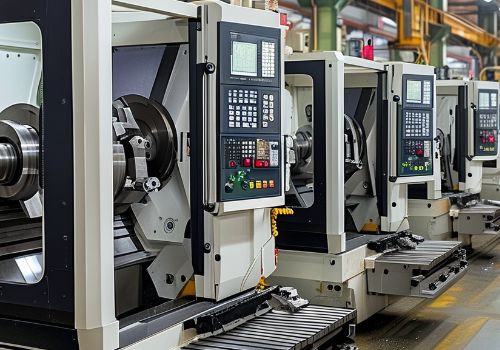
6. New Material Processing Capabilities
- As industries demand lighter and stronger materials (e.g., titanium alloys, advanced composites), CNC machining will evolve to accommodate these materials with enhanced tooling and cooling systems.
- Surface treatment technologies, like nano-coatings and self-healing materials, will gain traction to improve durability and reduce wear.
7. Customization and On-Demand Manufacturing
- Rising demand for custom and low-volume production will drive advancements in flexible CNC setups. Modular machines capable of quick reconfigurations will meet diverse production needs efficiently.
8. Regional Shifts in Manufacturing Powerhouses
- Asia-Pacific will continue to dominate as the largest market, with significant investments in high-tech manufacturing. China, India, and Southeast Asia will be key players.
- North America and Europe will maintain leadership in precision industries like aerospace and medical devices, focusing heavily on R&D and innovation.
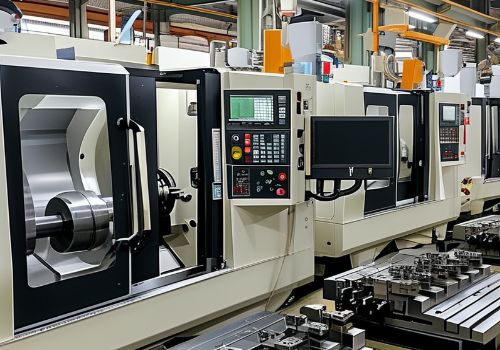
Challenges to Address
While these trends indicate significant opportunities, the industry must also address challenges such as:
- High capital investment for advanced machinery.
- A growing need for skilled operators and programmers.
- Cybersecurity risks associated with interconnected smart factories.
Strategic Implications
For companies to stay competitive, they should invest in:
- Training programs for workforce development.
- Research into sustainable and hybrid manufacturing solutions.
- Partnerships with tech providers for AI, IoT, and advanced tooling.
The CNC machining industry is set to become more intelligent, sustainable, and versatile by 2025, positioning itself as a cornerstone of modern manufacturing.
Ready to create your own custom CNC Machining parts? Contact us today to learn more about our CNC machining services and get a quote tailored to your needs!