In this era of high user experience, more and more mobile phones, notebooks, and wearable device manufacturers are beginning to exert their strength on the shell material. From the perspective of the mobile phone field, the material of the mobile phone shell is gradually transitioning from engineering plastics to metal.
There have been many combinations during the evolution of mobile phone shell material: plastic and metal, glass and metal, all plastic, all glass, etc., but all-metal material is more popular. From the actual touch experience, the all-metal mobile phone shell does have a superior experience in many aspects, no matter the appearance or feel, it is better than other materials.
When it comes to all metals, we must mention the CNC. At present, the full metal shell of 3C products is basically processed by CNC machines. CNC has become a must-have for 3C enclosure/shell/casing/housing manufacturers due to its high efficiency, high precision and stable processing quality.
The all-metal integrated CNC machining process was first created by Apple. The aluminum plate was die-cast from cylindrical solid aluminum. It was firstly cut into a prototype of a one-piece fuselage after precision machining. As the fuselage gradually formed, the shape of the keyboard on the fuselage And various fine structures are milled out. This process consists of a total of nine CNC milling processes, and a nine-pass process results in a precision one-piece shell.
Shell manufacturers need to go through roughing, semi-roughing, semi-finishing, finishing and other processes from programming to obtaining finished products. In many cases, more than 10 stations are needed to obtain finished products. And to improve the yield rate, very process needs to be tightly controlled.
CNC machining pre-processing work: modeling and programming
Before CNC machining begins, modeling and programming are first required. The difficulty of 3D modeling is determined by the product structure. Product modeling with complex structures is difficult, and the processes that need to be programmed are more and more complex. Programming includes machining process settings, tool selection, speed setting, distance per tool feed, and more. In addition, the clamping methods of different products are different, the fixtures must be designed before processing, and some complex structures require special fixtures.
Programming includes the processing technology of the whole product. Although the follow-up is completed by CNC automation, the pre-programming must be practiced by experienced personnel to avoid multiple trial and error to increase costs.
Main processing technology
The high-speed drilling center is used to accurately mill the aluminum sheet into a regular three-dimensional volume of a certain size, ready for the next process.
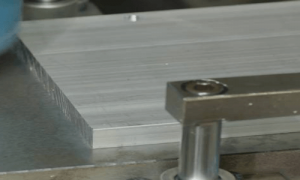
Rough milling: After positioning, the inner cavity structure is roughly milled, the positioning column combined with the clamp is clamped, and mill out most of the external redundant material.
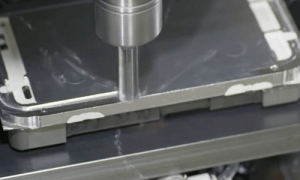
Milling antenna slot: The signal problem of the full metal shell is very difficult. It is necessary to mill out the antenna slot to leave a transmission path for the signal and maintain the necessary connection points to ensure the strength and overall sense of the fuselage.
CNC finishing: finishing the inner cavity, outer structure, outer surface, side edges, etc.
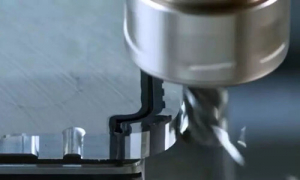
Polishing: Polishing with a high-speed precision CNC machine eliminates the milling marks and prepares for subsequent sand blasting.
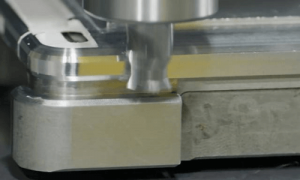
Sand blasting: The metal surface is treated to a matte finish.
Anodize treatment:
Primary anodize: color the phone, anodizing turns the aluminum into the color you need. At the same time improve the stability of the surface material.
Secondary anodize: the surface of the fuselage forms a strong and dense oxide film, and the wear resistance is further enhanced.
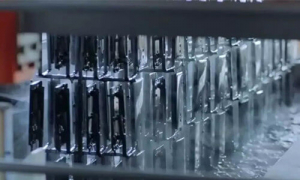
Plastic shell is molded by injection molding, and it can be mass-produced by simply opening the mold, and the yield is high. The CNC processing yield is determined by the structural complexity and accuracy requirements of the shell.
In order to balance the high cost, most manufacturers will choose to purchase a large number of CNC equipment when facing price wars, to reduce overall costs and meet productivity requirements.