In today’s fast-paced manufacturing landscape, reverse engineering has become a powerful tool that enhances the capabilities of CNC machining. Whether you’re recreating legacy parts, improving existing components, or solving design mysteries, reverse engineering plays a crucial role in transforming physical parts into digital models that can be accurately reproduced with CNC machines.
In this article, we’ll explore how reverse engineering is used in CNC machining, its benefits, applications, and why more companies are turning to this approach for high-precision manufacturing.
What Is Reverse Engineering in CNC Machining?
Reverse engineering is the process of deconstructing an existing part to analyze its design, dimensions, and functionality. The goal is to create a digital CAD model that can be used for replication, modification, or enhancement. This model then becomes the basis for producing identical or improved parts through CNC machining.
The process typically involves:
-
3D scanning or coordinate measuring (CMM) of the physical part
-
CAD model creation based on the scan data
-
CAM programming for CNC machines using the digital model
-
Precision machining of new parts from raw materials
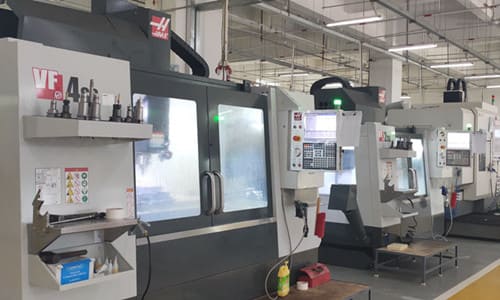
Why Use Reverse Engineering in CNC Machining?
Reverse engineering adds significant value to the CNC machining process by enabling manufacturers to replicate complex parts without access to original design files.
Key Benefits:
-
✅ Recreate discontinued or obsolete parts: Especially valuable in the automotive, aerospace, and machinery industries where old parts are no longer in production.
-
✅ Reduce product development time: Quickly capture the design of a physical prototype without starting from scratch.
-
✅ Enhance existing products: Analyze and improve an old design for better performance or reduced manufacturing costs.
-
✅ Cost savings: Avoid costly tooling or mold design by replicating parts directly through CNC machining.
-
✅ Competitive benchmarking: Understand competitor products and refine your own designs accordingly.
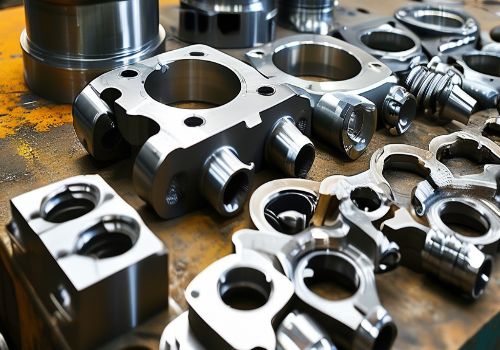
Industries That Benefit from Reverse Engineering with CNC
Several industries rely heavily on reverse engineering combined with CNC machining:
1. Automotive Aftermarket
Manufacturers often need to reproduce discontinued engine or body components. Reverse engineering enables accurate part duplication with modern materials and tighter tolerances.
2. Aerospace
Legacy aircraft often require exact-fit replacement parts. Reverse engineering ensures safety and compliance while using updated materials and CNC precision.
3. Medical Devices
Complex, patient-specific implants or surgical instruments can be reverse-engineered from prototypes or legacy devices and precisely machined to required specifications.
4. Industrial Machinery
When equipment breaks down and no blueprints are available, reverse engineering offers a fast, cost-effective path to produce compatible replacement parts.
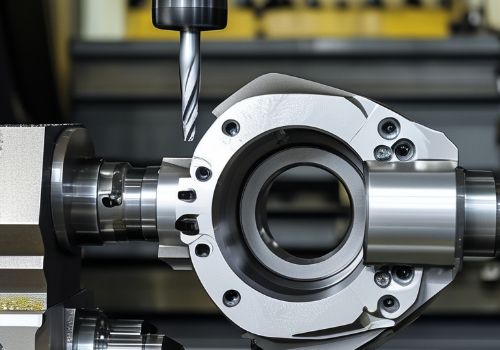
The Reverse Engineering Process for CNC Machining
Here’s how reverse engineering typically works in a CNC machining project:
Step 1: Part Scanning or Measurement
Using 3D laser scanners or coordinate measuring machines (CMMs), the part’s geometry is captured with high precision.
Step 2: CAD Model Generation
Specialized software reconstructs a digital 3D model, which can be reviewed, adjusted, or optimized for manufacturing.
Step 3: CAM Programming
Toolpaths are created using CAM software to guide CNC machines on how to cut or shape the part accurately.
Step 4: CNC Machining
The part is produced using 3-axis, 4-axis, or 5-axis CNC machines, depending on the complexity and tolerances needed.
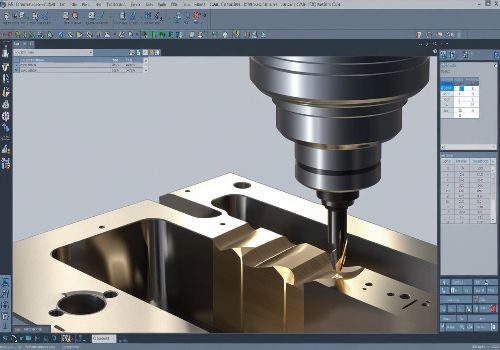
When Should You Use Reverse Engineering for CNC Projects?
You should consider reverse engineering in the following scenarios:
-
You have no access to original CAD files
-
You need to reproduce parts quickly
-
You want to improve upon an existing design
-
You’re looking to modernize production of an old component
-
You want to digitally archive your physical inventory for the future
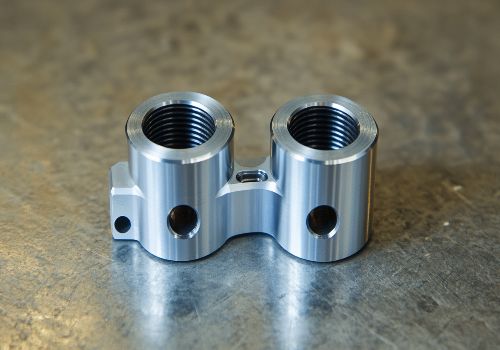
Conclusion: Reverse Engineering + CNC = Competitive Advantage
Reverse engineering isn’t just a problem-solving method—it’s a strategic advantage in modern CNC machining. By turning physical parts into accurate digital models, you unlock the ability to replicate, improve, and scale your production efficiently. It bridges the gap between legacy manufacturing and next-generation innovation.
At DO Machining, we offer comprehensive reverse engineering and CNC machining services, helping you digitize, redesign, and manufacture high-quality parts that meet your specifications. Whether it’s a legacy automotive part, custom prototype, or industrial machine component—we have the expertise to bring your project to life.
👉 Contact us today to explore how reverse engineering can benefit your business: https://www.domachining.com/