As long as screws are still present in machined parts, threads remain an important aspect of metalwork. It facilitates the connection of parts at a low cost, making them ideal for use with fasteners, fittings, and connectors. However, when making threaded holes, the finished threaded holes are not vertical enough has been a common problem.
To ensure the perpendicularity of a threaded hole during machining, we can follow these steps:
1. Proper Setup: Make sure the workpiece is properly secured in the machine to avoid any vibrations or movement during machining. Use appropriate clamps, fixtures, or chucks to hold the workpiece in place.
2. Tool Selection: Choose a high-quality cutting tool suitable for threading operations. The tool should have the correct geometry for creating precise threads and should be sharp to minimize any deflection.
3. Machine Calibration: Regularly calibrate your machining equipment to ensure its accuracy. This includes checking and adjusting the machine’s leveling, alignment, and spindle perpendicularity to the worktable.

4. Feed and Speed Rates: Use appropriate cutting speeds and feed rates as recommended by the tool manufacturer. Proper cutting parameters prevent excessive heat buildup and reduce the risk of tool deflection.
5. Coolant/Lubrication: Use an appropriate cutting fluid or lubricant during threading to reduce friction and heat generation. This can help maintain accuracy by preventing tool wear and deflection.
6. Stable Machining Conditions: Maintain stable machining conditions to minimize vibrations. Any unwanted vibrations can lead to inaccurate thread geometry and perpendicularity.
7. Tool Overhang: Minimize the tool overhang from the tool holder to reduce the risk of deflection. A shorter tool setup increases rigidity and accuracy.
8. Step-by-Step Approach: When machining deeper threaded holes, consider using a multi-pass approach. Gradually increase the depth of each pass to reduce the cutting forces and potential for deflection.
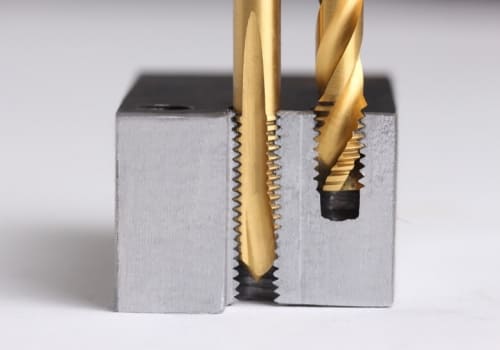
9. Tool Runout: Check for tool runout using appropriate measuring equipment. Excessive runout can negatively impact the accuracy of the threaded hole.
10. Post-Machining Inspection: After threading, use precision measuring instruments such as micrometers or dial indicators to measure the perpendicularity of the threaded hole. Compare the measurements to the required specifications.
11. Tool Maintenance: Regularly inspect and maintain your cutting tools. Dull or damaged tools can lead to deflection and poor thread quality.
12. Operator Skill: Ensure that the operator is well-trained and experienced in threading operations. Skilled operators can make real-time adjustments to minimize errors during machining.
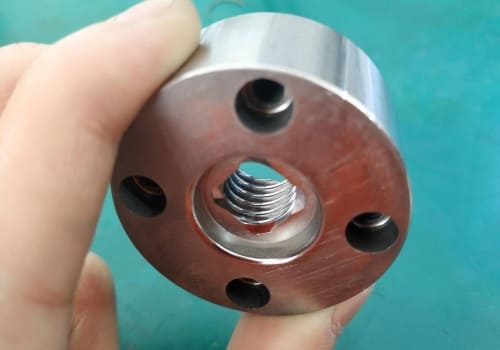
By carefully following these steps, we can help ensure the perpendicularity of threaded holes during machining and achieve accurate and high-quality results.
Ready to create your own custom CNC Machining parts? Contact us today to learn more about our CNC machining services and get a quote tailored to your needs!