In mechanical machining, how to machining small diameter deep holes is a common problem, and it is also a difficult problem to solve. The machining of small diameter deep holes generally adopts drilling machining. This article mainly summarizes and shares the common machining methods for small diameter deep holes.
1. Problems in machining small diameter deep holes
Small diameter deep hole machining is a closed state machining process, restricted by various external factors, small diameter deep hole machining process is very unstable, it is more difficult and complex than general hole machining. Various failures and problems often occur during machining, which affect the quality of the final product.
First, the drill bit for small diameter deep hole machining is easy to be broken.
Due to the small diameter of the deep hole, a slender drill has to be used. The smaller the drill, the lower the rigidity and strength, the worse the torque resistance, and the problem of offset or vibration is easy to occur, which greatly affects the machining accuracy.
Moreover, the machining of small diameter deep holes requires the spindle to have a high speed, the cutting force on the drill bit is large, and the drill bit is relatively small. It is difficult to ensure absolute symmetry when the two main cutting edges are sharpened, and in the case of unbalanced force, it is easy to break the drill bit. In addition, the high rotation speed of the drill bit generates high heat. Because the coolant is not easily injected into the cutting area due to the deep hole, the heat cannot be dissipated smoothly, and the drill core and the outer edge of the drill bit are easily burned under the action of high temperature.
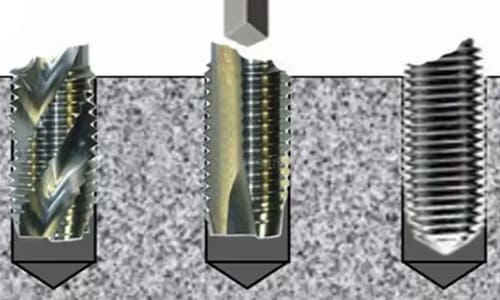
Second, the accuracy is difficult to control effectively.
Due to the limitation of conditions, small diameter deep hole machining cannot directly observe the cutting and cutting conditions of the tool, which increases the difficulty of machining process control.
Moreover, in the process of small diameter deep hole machining, the generated chips remain in the deep-hole, which is easy to block, aggravates the friction between the drill and the workpiece, and cannot be machined continuously, resulting in the accuracy of small diameter deep hole machining not meeting the requirements. If the material of the workpiece is relatively poor, such as the hardness, viscosity, and roughness of the material can not meet the machining requirements, when the drill encounters hard particles, it is prone to deflection, which will affect the accuracy requirements after machining.
2. Improvement of small diameter deep hole machining technology
A. Improvement of traditional twist drill technology
At present, most of the small diameter deep hole machining adopts traditional drilling, expanding, reaming and other methods. Due to the strict requirements on the tool for small diameter deep hole machining, not only the drill bit should be sharp, but also the angle between the drill bit and the main edge should be strictly equal, and the length of the main cutting edge should be consistent, otherwise it will occur problems such as inclination during machining, which will affect the machining accuracy. Among them, twist drill is the most commonly used method for small diameter deep hole machining.
In recent years, with the continuous improvement of mechanical machining technology, we have made many improvements to the traditional small diameter deep hole machining methods, the structural parameters of twist drills have been continuously optimized, and the machining stability and accuracy have become higher and higher. But some inherent sticking points remain difficult to resolve. For example, the axial resistance is large, the chips are too wide to remove, and the cutting fluid is difficult to inject. If we use manually inject cutting fluid, although the problem can be solved, the depth of each drilling is relatively shallow, and the drill must be repeatedly entered and exited. It not only affects the machining efficiency, but also greatly increases the burden on workers, so it is not suitable for large-scale machining.
In order to solve this problem, small and narrow grooves can be staggered on the flank of the two main cutting edges by appropriately increasing the top angle of the drill bit. This kind of chip splitter can reduce the cutting heat on the single edge with the same cutting amount, the length of the chip does not change, the chip volume becomes smaller, that is, the chip cross-sectional area becomes smaller, thus improving the chip evacuation and efficiency and cooling condition. Experiments show that this method can appropriately increase the amount of machining cutting, improve the machining efficiency, and prolong the service life of the drill bit.
B. Gun drilling for small diameter deep holes
Gun drilling is an efficient and economical method for machining small diameter deep holes. Gun drills consist of a drill bit with a V-shaped cutting edge and a cutting fluid hole, a drill rod and a drill shank designed for certain equipment. Gun drilling are suitable for mass production, and because it has high drilling efficiency and high precision, so it is widely used.
Gun drilling is a one-time feed deep hole drilling, and requires drilling of prefabricated hole, it has relatively high requirements on the workpiece. If the hardness and roughness of the workpiece to be machined do not meet the standards, the gun drilling method cannot be used at one time, and reaming must be performed in advance to meet the requirements.
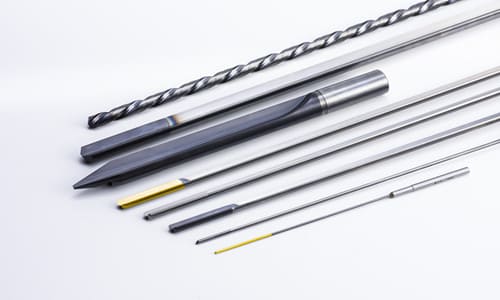
In actual production, it is difficult to carry out one-feed deep hole drilling in gun drilling machining. Most of them adopt the drilling method of graded feed. Place a moving block on the side of the machining mill, and design an outer diameter of 8*450 deep hole on it. The cutting fluid is sent from the oil inlet hole of the drill bit to the cutting area for cooling and lubrication. Sometimes workers do not know the cutting conditions in small diameter deep holes. Under the action of pressure, the chips sometimes cannot be washed away by the cutting fluid in time, which will cause the problem of the gun drill breaking. Therefore, the gun drilling process should maintain a high speed, and the guiding requirements of the tool at the beginning of drilling are high. If the spindle speed of the machining mill itself cannot meet the requirements of gun drilling, we can use the speed increaser to increase the speed.
C. Small diameter deep hole finishing technology
Small deep hole finishing is also known as the secondary machining of deep holes. Usually, after drilling or reaming for the first time, if the machining accuracy does not meet the expected requirements, it is necessary to carry out a second or more machining.
Usually, the deep hole machining parts that need to be finished are hydraulic cylinders, pump barrels, weapon launch tubes, instrumentation precision tubes, fluid pipes and sensor tubes with specific requirements, etc.
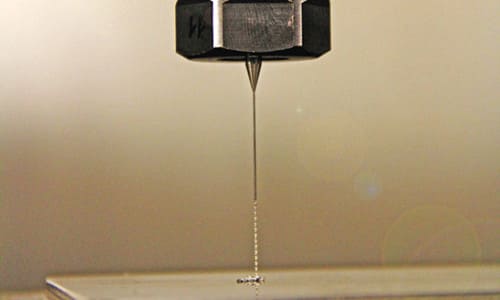
It is worth noting that since the small diameter deep hole finishing is secondary machining, it is machined on the basis of the original hole, so there is no problem such as chip removal, and the type of tool and the method of chips removal can be flexibly selected during the machining process. However, because the secondary machining is still carried out in the closed cavity of the hole, and it is affected by factors such as the length of the workpiece, the structure of the part, the size of the aperture, the stiffness of the workpiece and the stiffness of the guide rod, the difficulty of secondary machining of small deep holes is still higher than shallow holes machining.
At present, the common methods used in small deep hole finishing mainly include grinding, honing and electroplating honing. After years of research and development, the small diameter deep hole finishing technology has been continuously improved and innovated.
3. Conclusion
In a word, hole machining is the most common machining process in metal cutting, accounting for about 1/4 of the entire machining workload. Small diameter deep hole machining occupies a high proportion in hole machining. With the continuous development of machining technology, Small diameter deep hole machining has broad prospects for development.