In the world of custom CNC machining, cost and quality often seem at odds. Businesses want precision parts delivered fast, but they also need to stay within budget. Fortunately, with the right strategy, you can reduce CNC machining costs without sacrificing quality.
Whether you’re a startup building prototypes or an established company running full-scale production, this guide outlines practical tips to help you optimize your machining projects and achieve cost-effective, high-quality results.
1. Optimize Your Part Design
One of the most effective ways to reduce CNC machining costs is to simplify the part design. Complex geometries, sharp internal corners, and deep cavities may look great in CAD, but they significantly increase machining time and tool wear.
✅ Design for Manufacturability (DFM) Tips:
-
Use standard hole sizes
-
Avoid unnecessary tight tolerances
-
Eliminate undercuts if possible
-
Minimize the number of setups needed
The simpler the part, the less time it takes to machine—and the lower your cost.
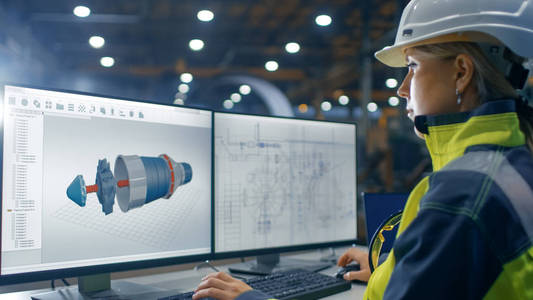
2. Choose the Right Material
Material selection can greatly affect both cost and machining speed. Some metals and plastics are easier to machine than others. For instance, aluminum is more cost-effective than titanium or stainless steel due to its machinability.
💡 Tip:
If strength and aesthetics allow, opt for materials that are easier to cut and finish. This reduces tool wear and speeds up production.
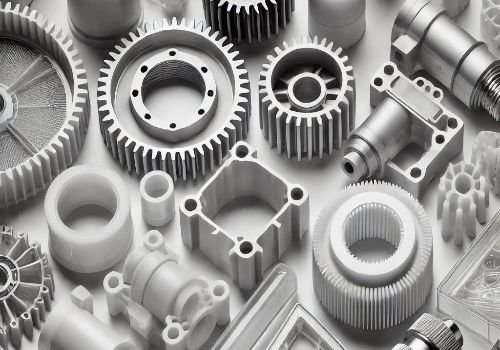
3. Order in Higher Volumes
While CNC machining is perfect for both low and high volumes, larger orders typically lower the cost per part. Setup time is a major cost driver—once the machine is programmed and calibrated, running additional parts is much faster and more efficient.
📉 Bulk Ordering Advantages:
-
Reduced setup costs per unit
-
Better material usage
-
Volume discounts from suppliers
If you expect to need more parts in the future, consider ordering a larger batch.
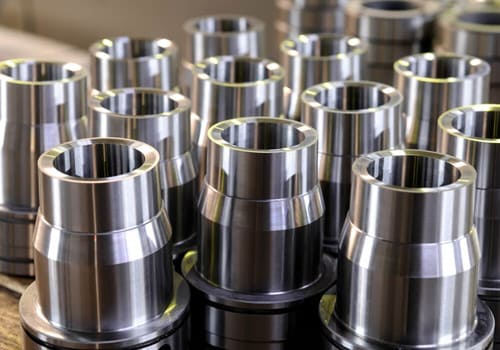
4. Consolidate Parts or Operations
When possible, combine multiple components into a single machined part to reduce the number of assemblies and processes. Also, working with a provider that offers one-stop services (like machining, finishing, and assembly) helps cut coordination and logistics costs.
At DO machining, we offer full-service CNC solutions, including anodizing, plating, and inspection—all under one roof.
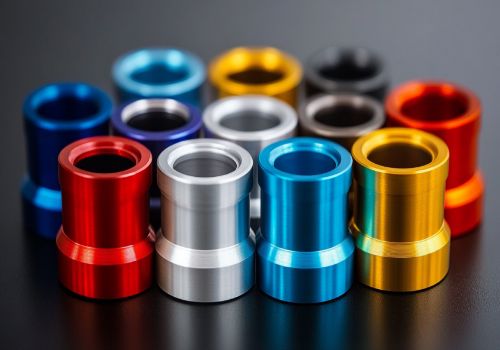
5. Use Tolerances Wisely
Tight tolerances are necessary in some applications, but don’t apply tight tolerances everywhere by default. They often require slower cutting speeds, specialized tools, and additional inspections—all of which add to the price.
🎯 Pro Tip:
Clearly communicate which dimensions are critical to function and which are less important. Let your machining partner optimize the rest
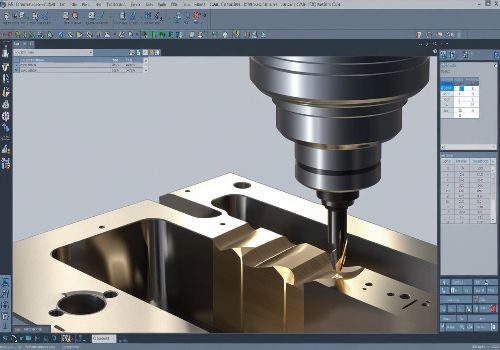
6. Eliminate Unnecessary Surface Finishes
Post-processing, like anodizing, powder coating, or polishing, can improve appearance or corrosion resistance—but they also add cost. If your part doesn’t require a cosmetic finish or if it’s used internally, you may be able to skip or simplify finishing processes.
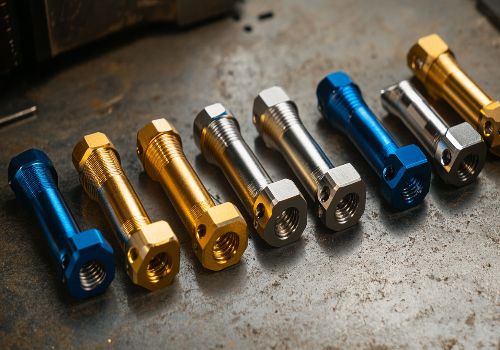
7. Partner With an Experienced CNC Machining Company
Ultimately, working with a reliable and experienced CNC machining service provider can save you more money than cutting corners on quality. Skilled engineers will help you optimize designs, select cost-effective materials, and avoid costly design flaws before production begins.
At DO Machining, we’ve helped clients in automotive, electronics, and industrial sectors reduce costs while maintaining tight tolerances and high performance.
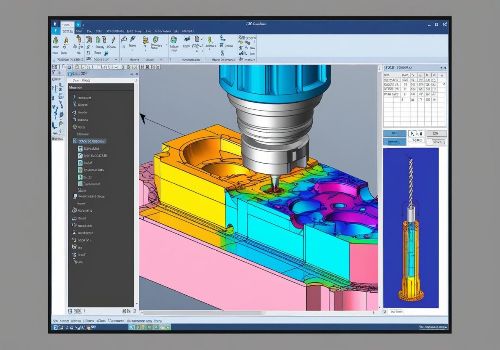
Conclusion
Lowering CNC machining costs doesn’t mean compromising quality. With smart design decisions, careful material choices, and the right manufacturing partner, you can optimize your project and improve ROI.
If you’re looking for cost-effective, high-quality CNC machining services, contact us today. Let’s work together to bring your next project to life—on time and on budget.
👉 Explore our CNC services here: www.domachining.com