CNC machining is widely known for its precision and efficiency. However, even with advanced technology, errors can still occur during machining, leading to wasted materials, delays, and increased costs. This blog provides actionable tips and best practices to help reduce errors in CNC machining and ensure high-quality results every time.
1. Common CNC Machining Errors and Their Impact
Misaligned Tools
Misaligned cutting tools can cause inaccurate cuts, resulting in parts that don’t meet specifications.
Programming Errors
Errors in the CNC code (G-code) can lead to incorrect tool paths, causing machining defects.
Material Issues
Incompatible or low-quality materials can lead to surface defects, tool wear, or dimensional inaccuracies.
Operator Mistakes
Human errors, such as incorrect machine setup or improper tool handling, often lead to machining failures.
2. Best Practices to Minimize CNC Machining Errors
a) Optimize CAD and CAM Design
- Ensure the CAD model is error-free and well-designed for machining.
- Use simulation tools in CAM software to verify tool paths and identify potential issues before machining begins.
b) Use High-Quality Tools and Materials
- Invest in precision cutting tools made from durable materials.
- Choose raw materials with consistent quality to minimize machining challenges.
c) Maintain and Calibrate CNC Machines Regularly
- Regular maintenance ensures all machine components function correctly.
- Frequent calibration minimizes tool misalignment and mechanical wear.
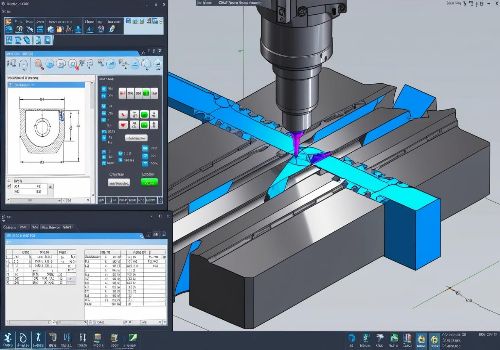
3. Programming Tips for Error Reduction
a) Use Accurate G-Code
- Double-check your G-code to ensure it matches the part design.
- Avoid manual programming errors by relying on automated CAM software.
b) Include Safety Checks
- Add tool change verification and collision detection to your CNC programs.
- Include appropriate feed rates and speeds based on material properties.
4. Quality Control Measures
a) Use Advanced Inspection Tools
- Incorporate Coordinate Measuring Machines (CMM) to verify dimensions and tolerances.
- Use laser scanners for non-contact inspection of complex surfaces.
b) Test Prototypes Before Full Production
- Run a prototype or sample batch to identify potential errors early.
- Compare prototypes with CAD models to verify accuracy.
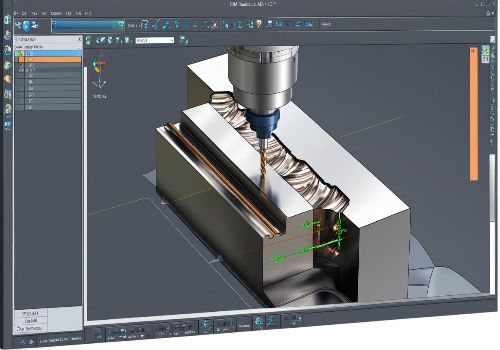
5. Operator Training and Skill Development
a) Provide Comprehensive Training
- Train operators on machine setup, programming, and maintenance.
- Keep them updated on the latest CNC machining trends and technologies.
b) Encourage Collaboration
- Foster communication between designers, machinists, and quality control teams to identify and resolve issues collaboratively.
6. Embrace Automation and AI Integration
a) Use Predictive Maintenance Systems
- Leverage AI to monitor machine health and predict when maintenance is needed.
b) Automate Repetitive Tasks
- Automate tasks like tool changes and material handling to minimize human error.
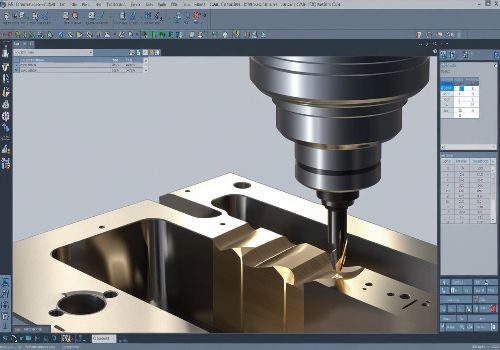
7. Conclusion
Reducing errors in CNC machining is vital for achieving high-quality results and minimizing costs. By following these best practices—ranging from optimizing CAD/CAM design to maintaining equipment and ensuring operator expertise—you can significantly enhance the precision and efficiency of your CNC machining processes.
At domachining.com, we specialize in error-free CNC machining solutions tailored to your industry needs. Contact us today to learn more about how we can help you achieve precision in your manufacturing projects.