CNC (Computer Numerical Control) machining is an essential manufacturing process that produces precise and intricate parts for various industries. While many businesses turn to CNC machining for its accuracy and efficiency, the cost of CNC machining can vary significantly based on a range of factors. In this blog, we’ll break down the true cost of CNC machining, what influences it, and how you can manage costs effectively for your projects.
1. Understanding the Factors That Affect CNC Machining Costs
CNC machining may seem like a straightforward process, but many factors influence its cost structure. Understanding these variables is crucial to estimating and managing your machining budget.
a) Material Selection
The choice of material has a significant impact on the cost of CNC machining. Materials such as stainless steel, titanium, and Inconel are more expensive due to their hardness, machining difficulty, and material costs. On the other hand, softer materials like aluminum and plastics are easier to machine and more cost-effective.
b) Part Complexity
The complexity of the part you need will influence both machining time and tooling costs. Parts with intricate geometries or tight tolerances often require longer machining times, specialized tooling, and more advanced CNC machines (e.g., 5-axis machines). The more complex the part, the higher the cost.
c) Tolerances and Finish Requirements
Parts with strict tolerance requirements or specialized surface finishes (such as anodizing, polishing, or plating) generally incur higher costs. Achieving high precision requires advanced CNC equipment and additional post-processing, which can increase time and material usage.
d) Batch Size
For low-volume runs or one-off prototypes, the setup and tooling costs are generally higher because the machine needs to be reset for each part. On the other hand, high-volume production reduces the per-unit cost due to the efficiency of automated systems and less downtime for machine setup.
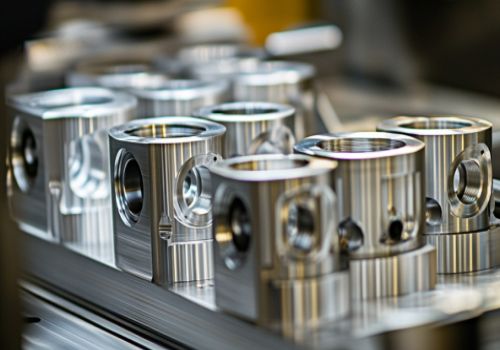
2. Key Cost Components in CNC Machining
Now that you have an understanding of the factors involved, let’s break down the major cost components:
a) Setup Costs
Setup costs are incurred when preparing the machine to produce the parts. This includes loading the program into the CNC machine, securing the material, and calibrating the machine. For highly complex parts, setup time can be substantial, making it a significant cost factor in low-volume production.
b) Machine Time
CNC machining is a time-intensive process, and the longer the machine runs, the higher the cost. Machine time includes the actual cutting time, along with time for setup, tool changes, and potential tool wear. The complexity of the part and the type of machine being used will directly affect machine time.
c) Tooling Costs
Specialized tools are often required for machining certain parts, especially when dealing with hard materials or intricate designs. Tooling costs may include the purchase of new tools or the maintenance and replacement of existing tools.
d) Labor Costs
Labor costs may include the wages of machinists, engineers, and operators who program the CNC machine, monitor its operation, and inspect the finished parts. For high-precision work, experienced labor is essential, which can add to the overall cost.
e) Post-Processing Costs
Many parts require post-processing, including operations like deburring, polishing, coating, or heat treatment. These steps can add time and cost, especially if they require manual intervention. The more intricate the finish, the higher the cost.
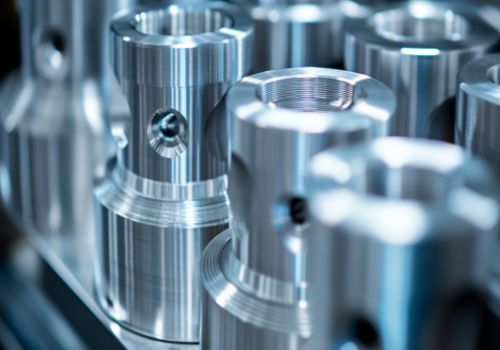
3. How to Reduce the Cost of CNC Machining
While CNC machining offers excellent precision, it’s important to find ways to manage and reduce costs. Here are some strategies that can help you achieve high-quality parts without exceeding your budget:
a) Optimize Your Design for Manufacturability
Designing parts that are easy to machine can significantly reduce costs. Avoid overly complex geometries, unnecessary features, and tight tolerances that require additional machining. Work with your design team or a CNC expert to optimize your designs for cost-efficient production.
b) Choose the Right Material
Choosing the right material is critical to controlling costs. While premium materials may be necessary for certain applications, it’s often possible to achieve the desired performance with a less expensive alternative. Consider material properties, strength, and durability when selecting the best material for your project.
c) Use Standardized Tooling
If possible, use standardized tooling to avoid the additional costs of custom tools. Custom tools are often more expensive and can increase both setup time and machine time. Using commonly available tools can help keep costs under control.
d) Opt for High-Volume Production
If you need a large number of parts, high-volume production often results in lower per-unit costs due to economies of scale. Once a CNC machine is set up and calibrated, the cost per part decreases with each additional unit produced. If you have ongoing production needs, batching orders can help minimize costs.
e) Consider Automation
Incorporating automation into the machining process—such as automated tool changers, loading systems, and robotic arms—can reduce labor costs and increase machining efficiency, leading to cost savings over time.
4. Hidden Costs in CNC Machining
While the major cost components of CNC machining are easy to spot, there are also hidden costs that can catch you by surprise. These include:
- Shipping Costs: If you’re outsourcing CNC machining, shipping costs for materials and finished parts can add up.
- Setup Fees: Some CNC machining companies charge separate fees for initial setup, especially for smaller or custom orders.
- Design Modifications: Changes to the design after production has started can lead to additional costs, as machines may need to be recalibrated or reprogrammed.
5. Conclusion: The Key to Managing CNC Machining Costs
CNC machining is an indispensable process in modern manufacturing, but understanding its costs is essential for effective project management. By considering factors such as material choice, part complexity, tolerances, batch size, and machine time, you can manage costs more effectively. Additionally, optimizing your design for manufacturability, leveraging automation, and partnering with a reliable CNC supplier can help keep your machining costs under control.
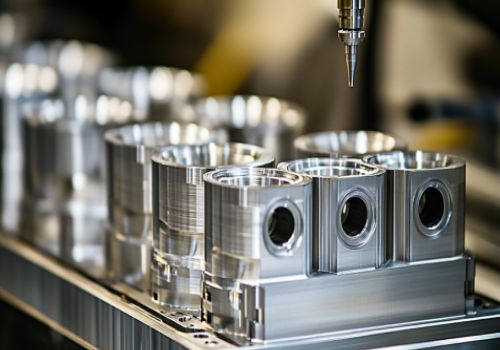
At domachining.com, we’re committed to providing high-quality CNC machining services at competitive prices. Whether you need prototypes, low-volume runs, or large-scale production, we have the expertise and technology to meet your needs. Contact us today to learn how we can help you achieve high-quality, cost-effective CNC machined parts.