In the manufacturing world, efficiency, precision, and cost-effectiveness are critical factors in choosing a production method. CNC (Computer Numerical Control) machining has emerged as a frontrunner due to its ability to produce high-quality parts with minimal post-processing compared to other manufacturing techniques. But why does CNC machining require less post-processing? Let’s dive into the details.
1. High Precision from the Start
CNC machining is renowned for its unmatched precision. With tolerances often as tight as ±0.001 inches, CNC machines can produce parts that meet exact design specifications on the first try. Advanced programming and the use of cutting-edge tools ensure the desired shapes and finishes are achieved during the machining process itself. This minimizes the need for additional steps such as grinding, polishing, or resizing, which are often required in traditional manufacturing methods.
2. Superior Surface Finish
A significant factor contributing to reduced post-processing is the exceptional surface finish that CNC machining offers. Depending on the material and cutting parameters, CNC-machined parts often achieve surface finishes as smooth as 32 Ra (Roughness Average) or better. Advanced multi-axis machines and high-speed cutting tools further enhance the smoothness, eliminating or drastically reducing the need for secondary polishing or sanding.
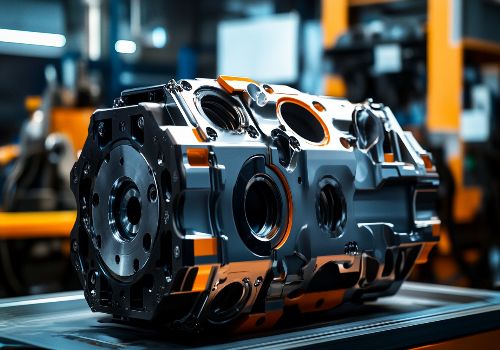
3. Wide Range of Compatible Materials
CNC machining is compatible with a broad spectrum of materials, including metals, plastics, and composites. Unlike methods such as casting or injection molding, CNC machining does not introduce imperfections like flash, seams, or surface inconsistencies. This versatility ensures that even challenging materials like titanium or hardened steel are machined with minimal defects, eliminating the need for extra cleaning or refining.
4. Custom Tooling and Precision Programming
CNC machines rely on CAD (Computer-Aided Design) and CAM (Computer-Aided Manufacturing) software to guide their operations. This combination allows manufacturers to customize tooling and programming for each specific part. By tailoring the cutting path, tool geometry, and machining speed, CNC systems produce parts that require little to no rework. This level of customization is challenging to achieve with other methods like 3D printing or manual machining.
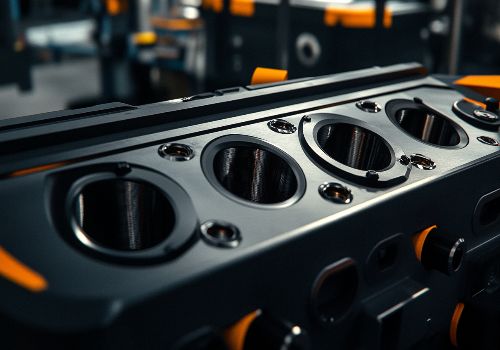
5. Elimination of Defects Common in Other Methods
Manufacturing methods such as casting or welding often introduce defects like porosity, warping, or uneven surfaces, which necessitate extensive post-processing. CNC machining, however, avoids these issues by employing a subtractive process. This ensures parts are free of internal defects, edges are sharp and clean, and dimensions are consistent, reducing the need for additional corrective measures.
6. Advanced Capabilities for Complex Geometries
Multi-axis CNC machines can handle complex geometries and intricate designs with ease. These machines can perform multiple operations—such as drilling, milling, and turning—in a single setup, which minimizes the risk of misalignments or dimensional inaccuracies. As a result, parts are closer to their final form upon completion, requiring little or no post-processing.
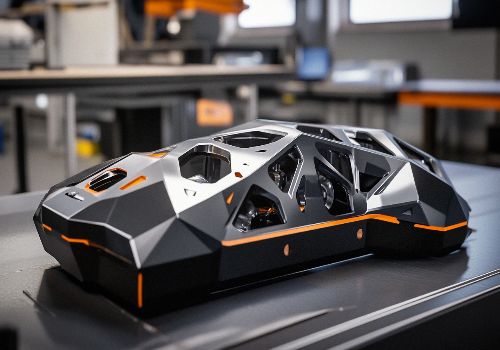
7. Efficient Surface Treatments Integrated into the Process
Modern CNC machining often integrates surface treatments like anodizing, coating, or deburring as part of the workflow. This eliminates the need for external processes, ensuring parts are production-ready as soon as they come off the machine.
Conclusion
CNC machining has revolutionized the manufacturing industry by delivering unparalleled precision, efficiency, and quality. Its ability to produce parts that require minimal post-processing not only saves time but also reduces costs and improves overall productivity. For manufacturers seeking reliable and cost-effective solutions, CNC machining offers a clear advantage over other methods.
By investing in CNC technology, manufacturers can streamline their production processes, minimize waste, and deliver superior products with shorter lead times—proving once again why CNC machining is the gold standard in modern manufacturing.
If you found this guide helpful, explore our other blogs for more insights into CNC machining techniques and their benefits. And if you’re ready to take your manufacturing to the next level, feel free to reach out to us at www.domachining.com!